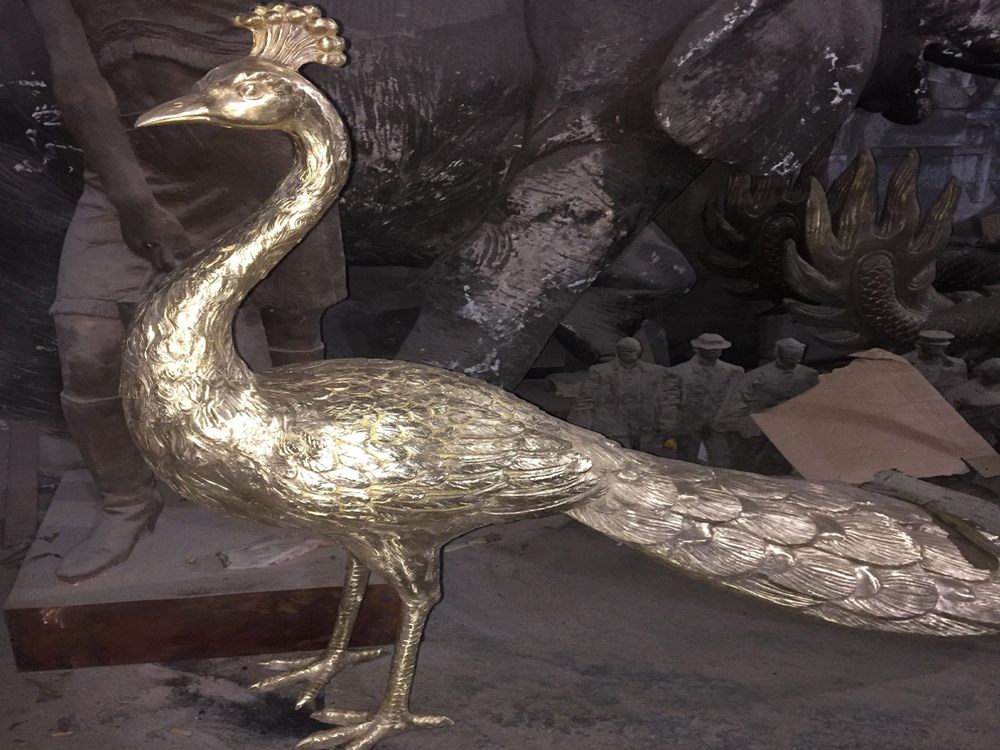
Dezincification, a selective leaching process that removes zinc from bronze alloys, significantly weakens their structural integrity. To combat this issue in high-zinc bronze alloys, several proven methods can be employed.
1. Alloy Composition Adjustment: Reducing zinc content below 15% or adding small amounts of arsenic (0.02-0.1%), antimony, or phosphorus creates a more stable microstructure resistant to selective corrosion.
2. Protective Coatings: Applying epoxy, polyurethane, or nickel plating forms a physical barrier against corrosive elements. Regular maintenance of these coatings is crucial for long-term protection.
3. Cathodic Protection: Connecting the alloy to a sacrificial anode (like magnesium or zinc) forces the protected metal to become the cathode in an electrochemical cell, preventing dezincification.
4. Environment Control: Maintaining neutral pH levels (6-8) in surrounding fluids and avoiding stagnant water conditions significantly reduces corrosion risks.
5. Heat Treatment: Proper annealing at 550-650°C followed by controlled cooling can optimize the alloy's microstructure for better corrosion resistance.
For critical applications, combining multiple methods provides the most reliable protection. Regular inspection using microscopic analysis or weight-loss measurements helps detect early signs of dezincification before structural damage occurs.