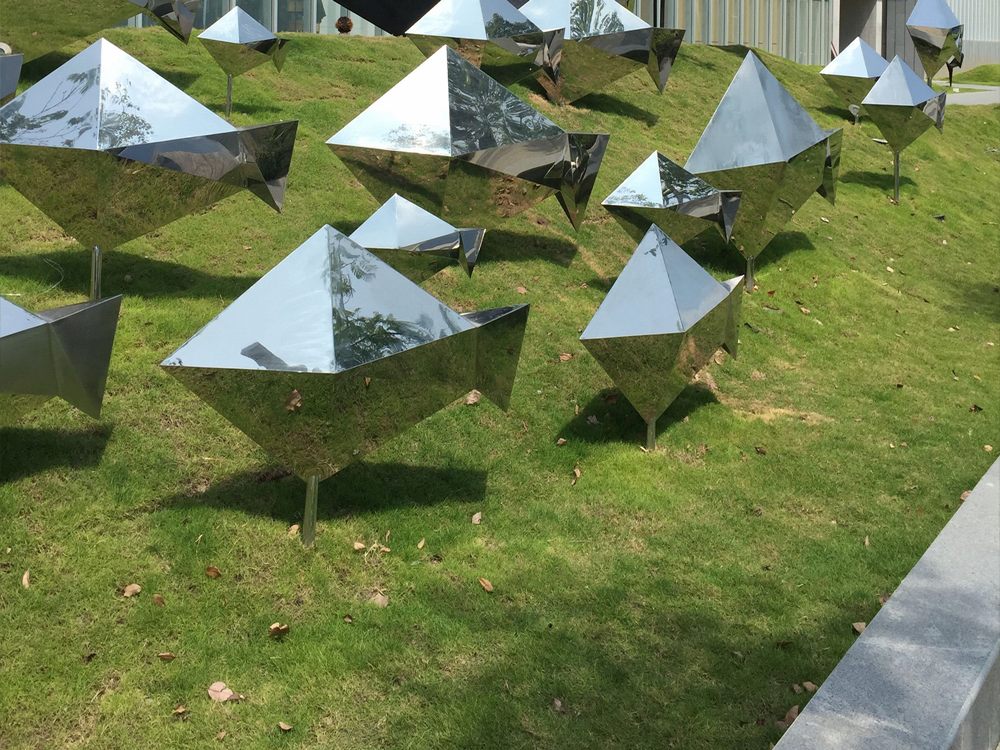
Creating large bronze sculptures is a complex interplay of artistry and engineering. To ensure structural integrity, artists employ meticulous techniques from design to installation.
The process begins with a robust internal framework, often made of stainless steel or reinforced armatures, which provides core support. Engineers and sculptors collaborate to calculate weight distribution, wind resistance, and load-bearing capacity, especially for outdoor installations.
During metal casting, the lost-wax method remains a gold standard. Artists create detailed wax models, which are then encased in ceramic molds before molten bronze is poured. The thickness of bronze walls is carefully controlled—typically 3-8mm—to balance durability with weight limitations.
Modern techniques include finite element analysis (FEA) to simulate stress points digitally before fabrication. Many sculptors now incorporate hollow casting methods with internal cross-bracing, significantly reducing weight while maintaining strength.
For monumental works, segmented casting is common. Large sculptures are cast in manageable sections, then expertly welded together using bronze-specific techniques that preserve both structural and aesthetic continuity.
Finally, strategic anchoring systems are engineered for permanent installations. Stainless steel mounting plates, seismic considerations, and corrosion-resistant hardware ensure decades of stability against environmental forces.
Through this fusion of ancient craftsmanship and modern engineering, bronze sculptures achieve both artistic vision and enduring structural soundness.