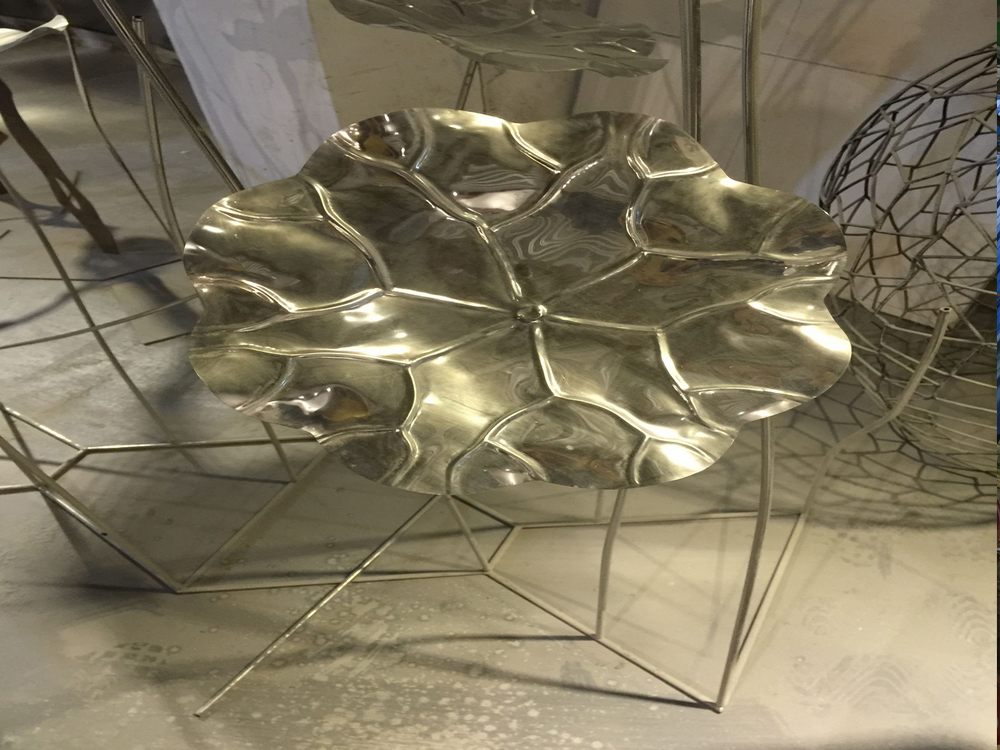
Mass-produced bronze sculptures, while often more affordable than handcrafted pieces, are prone to several common defects due to the industrial casting process. One frequent issue is porosity, where tiny air bubbles become trapped during casting, leaving small holes or weak spots in the sculpture. Another common flaw is incomplete filling, where molten bronze fails to reach all parts of the mold, resulting in missing details or uneven surfaces.
Surface imperfections like rough patches, uneven textures, or visible seam lines from mold joints are also prevalent in mass-produced pieces. These defects often require additional finishing work, which may not always be meticulously done in large-scale production. Additionally, inconsistent patinas—the colored finishes applied to bronze—are a frequent complaint, with uneven tones or poorly adhered coatings that may flake over time.
Structural weaknesses, such as thin or brittle sections, can occur when manufacturers prioritize speed over quality control. Finally, misaligned parts or asymmetrical features may appear in sculptures assembled from multiple cast components. While these defects don’t always diminish the artistic value, they can significantly affect the durability and aesthetic appeal of mass-produced bronze artworks.