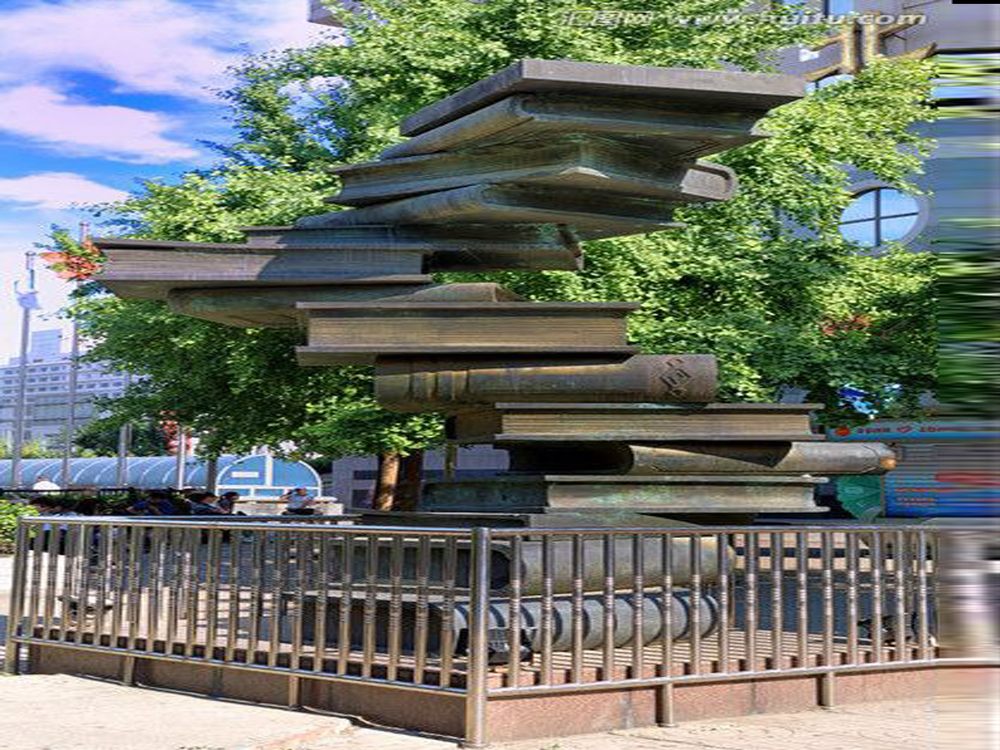
Bronze casting is a timeless art form with two distinct approaches: studio-foundry and industrial methods. While both share the same fundamental metalworking principles, their purposes, scales, and techniques diverge significantly.
Studio-foundry casting is the realm of artists and small workshops, prioritizing creative expression and craftsmanship. Each piece is individually crafted using labor-intensive techniques like lost-wax casting, often involving hand-finishing and patination. The process allows for artistic experimentation, with typical outputs including sculptures, decorative items, and limited edition artworks. Production capacity is limited, usually handling just a few pieces at a time.
Industrial bronze casting focuses on mass production and functional components. Utilizing automated processes and standardized molds, factories can produce hundreds of identical parts daily. The emphasis is on efficiency, consistency, and meeting technical specifications rather than artistic merit. Common applications include machinery parts, architectural elements, and industrial components requiring bronze's durability.
Key differences emerge in several areas:
1. Scale: Studio work produces single pieces; industry manufactures batches
2. Tools: Artists use manual tools; factories employ heavy machinery
3. Tolerances: Industrial casting demands precise engineering specs
4. Surface quality: Studio pieces value texture; industrial parts need smooth finishes
5. Patinas: Artistic works use varied finishes; industrial pieces often skip this step
Understanding these distinctions helps creators and buyers choose the right approach for their needs, whether pursuing artistic vision or functional requirements. Both methods preserve bronze casting's legacy while serving different sectors of modern demand.