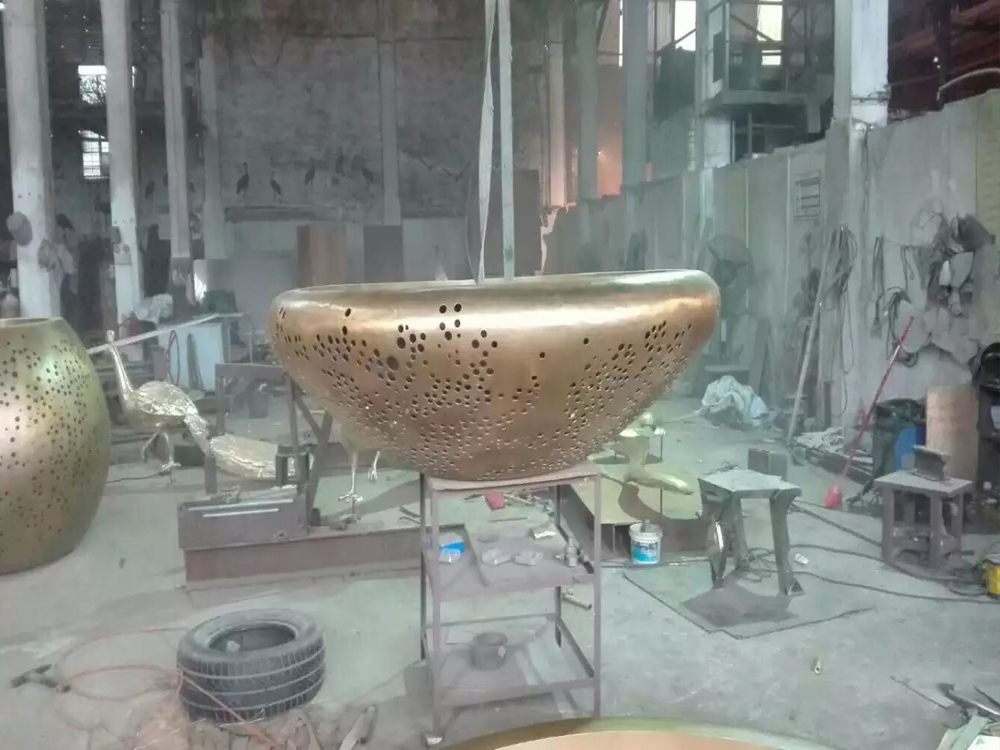
Creating bronze sculptures with integrated timekeeping mechanisms represents a fascinating intersection of art and engineering, presenting unique challenges that test both creative vision and technical skill. The first major hurdle lies in material compatibility – bronze expands and contracts with temperature changes, which can disrupt the delicate mechanics of clockwork components. Sculptors must account for these thermal dynamics when designing the internal cavities to house the mechanism.
Precision casting poses another significant obstacle. Unlike traditional sculptures, these works require millimeter-perfect hollow spaces to accommodate gears and springs without compromising structural integrity. Foundry techniques must be adapted to create these precise negative spaces while maintaining the sculpture's artistic form.
The weight distribution challenge emerges as bronze's density can strain clock mechanisms not designed for such loads. Artists often need to collaborate with horologists to reinforce or modify movements. Additionally, the patination process – crucial for bronze's aesthetic appeal – must avoid corrosive chemicals that could damage the timekeeping components.
Perhaps most complex is achieving artistic harmony between the sculptural form and functional elements. The clock face or visible components must feel organically integrated rather than added as an afterthought. This demands careful planning from the initial design phase through final assembly.
Successful execution requires mastery of multiple disciplines: metallurgy for the bronze, mechanical engineering for the clockwork, and artistic sensibility to unify these elements. Those who overcome these challenges create remarkable works that transcend both sculpture and timepiece, offering viewers a unique experience where art measures the passage of time itself.