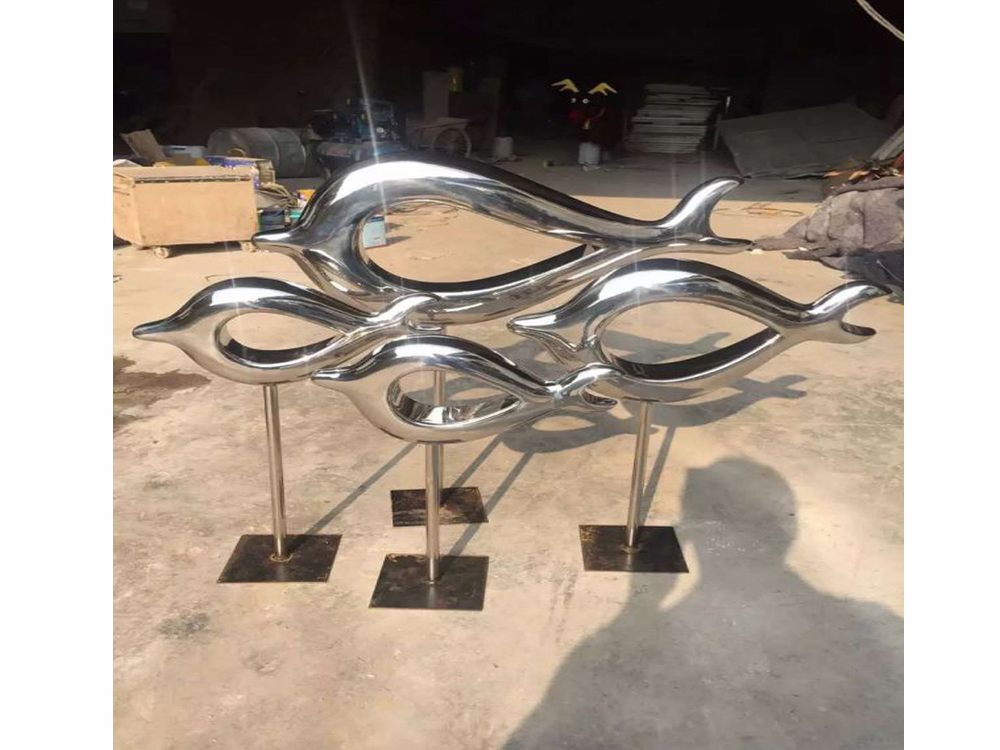
Creating bronze sculptures with fine details requires a combination of ancient techniques and modern precision. Artists typically begin with the lost wax casting method, where every minute detail is first carved into a wax model. This fragile original captures even the finest textures and patterns that will later appear in metal.
The wax model is then encased in a ceramic shell through multiple dipping processes. Each layer must be carefully applied to preserve the delicate features. When molten bronze is poured into the mold, it perfectly replicates these intricate details as it replaces the melted wax.
After casting, artists employ various finishing techniques to enhance the sculpture's details. Chasing involves carefully refining the metal surface with specialized tools to sharpen lines and textures. Patination, the chemical coloring process, further accentuates details through controlled application of heat and chemicals that create contrasting tones.
Modern sculptors sometimes combine traditional methods with contemporary technologies like 3D printing to create initial models with microscopic precision. However, the human touch remains essential in final adjustments where artists manually refine each element to achieve artistic perfection.
The entire process demands extraordinary patience and skill, with master sculptors spending hundreds of hours on a single piece to ensure every hair, wrinkle, or feather appears with breathtaking realism in the final bronze work.