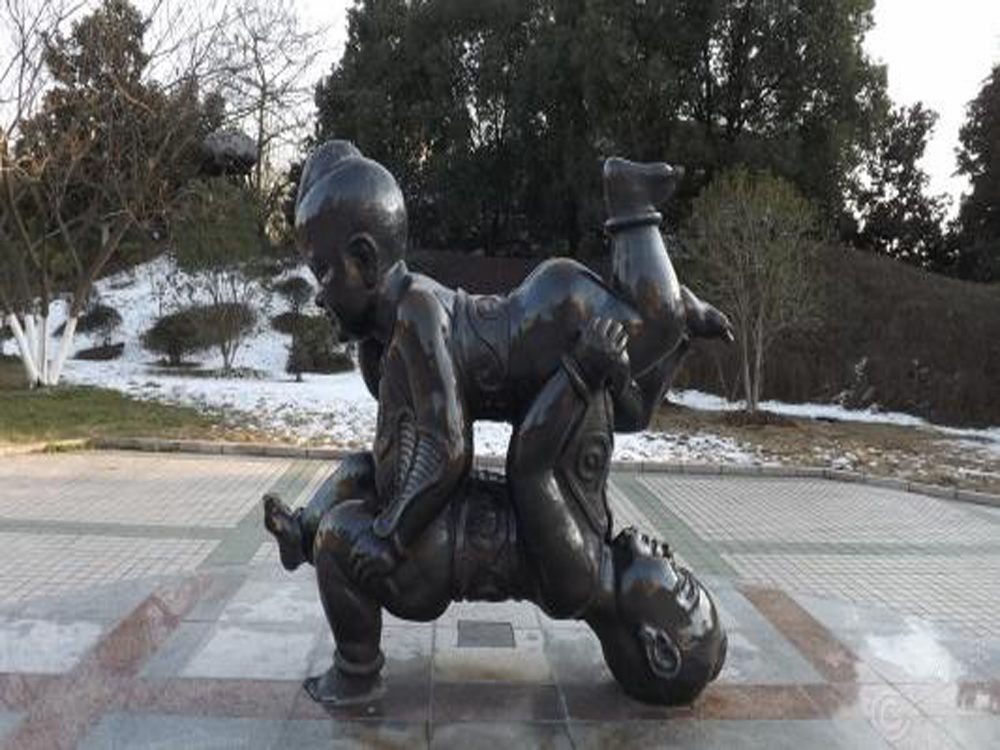
Bronze sculptures stand as timeless testaments to the harmonious intersection of art and engineering. These masterpieces are not merely artistic expressions but also feats of technical precision, requiring a deep understanding of materials, physics, and craftsmanship.
The creation of bronze sculptures begins with meticulous design, where artists translate abstract ideas into tangible forms. This phase demands both artistic vision and engineering foresight, as the design must account for structural stability and the behavior of molten metal during casting. The lost-wax casting technique, a hallmark of bronze sculpture, exemplifies this synergy. Artists sculpt a wax model, which is then encased in a ceramic mold. Once the wax is melted away, molten bronze is poured into the cavity, solidifying into the desired shape. This process blends artistic detail with metallurgical expertise.
Engineering principles also play a crucial role in ensuring the longevity of bronze sculptures. Factors like weight distribution, thermal expansion, and environmental resistance are carefully considered to prevent cracks or deformities over time. The patina, a chemically induced surface finish, not only enhances aesthetics but also protects the metal from corrosion—a perfect marriage of art and science.
Ultimately, bronze sculptures embody the collaborative spirit of creativity and precision. They remind us that great art is often underpinned by rigorous engineering, and that innovation thrives at the intersection of disciplines.