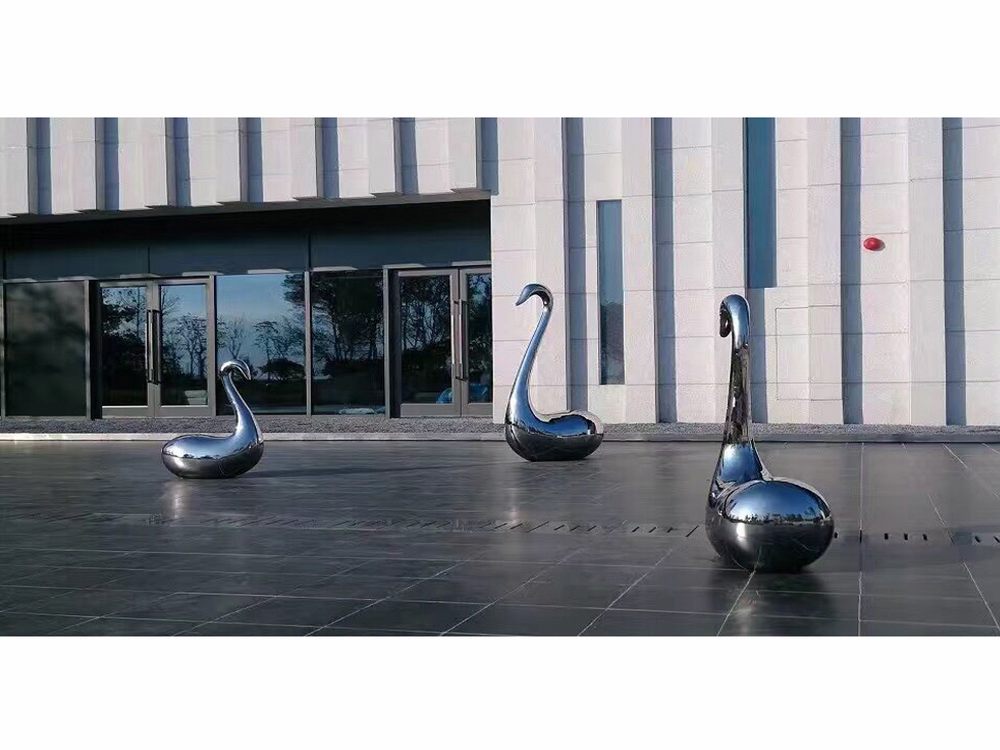
Bronze castings are prized for their durability and aesthetic appeal, but surface imperfections can sometimes occur during the casting process. The most common defects include porosity, shrinkage cavities, cold shuts, misruns, and surface roughness.
Porosity appears as tiny holes caused by trapped gas or improper cooling. To fix it, welders often use bronze filler rods to fill the voids, followed by careful grinding and polishing. Shrinkage cavities, larger depressions formed during cooling, require similar repair methods but may need additional material buildup.
Cold shuts and misruns – incomplete fusions or unfilled mold sections – typically demand recasting or skilled TIG welding to blend the flawed areas seamlessly. Surface roughness, often from mold issues or improper finishing, can be corrected through sanding, buffing, or chemical treatments.
For optimal results, professionals combine mechanical and chemical finishing techniques. Sandblasting prepares surfaces, while patina applications can hide minor flaws. Electroplating offers another solution for both cosmetic enhancement and protection.
Preventative measures like proper mold design, controlled cooling rates, and high-quality materials significantly reduce imperfections. When defects do occur, modern restoration techniques can return bronze castings to their intended glory, preserving both function and beauty.