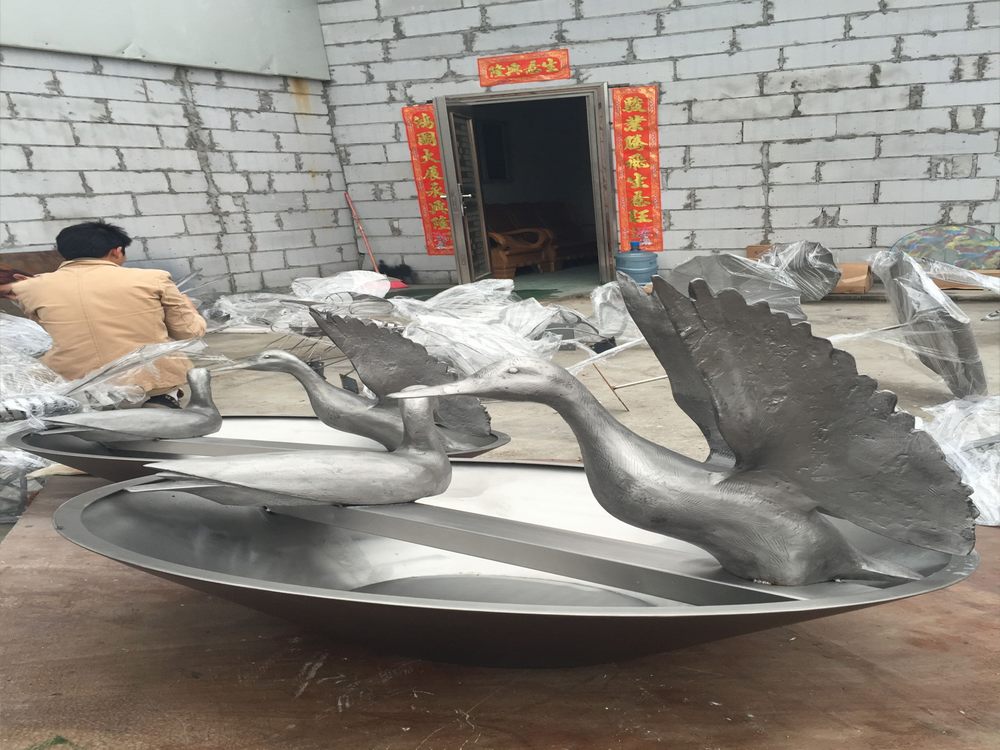
Oxidation during the casting process can significantly degrade the quality of metal products, leading to defects like porosity and weakened structural integrity. To combat this, here are the most effective methods to prevent oxidation:
1. Use of Protective Atmospheres: Inert gases like argon or nitrogen can be introduced into the casting environment to displace oxygen, minimizing oxidation.
2. Flux Application: Applying fluxes such as borax or silica creates a protective layer over molten metal, shielding it from oxygen exposure.
3. Vacuum Casting: This advanced technique removes oxygen entirely from the casting chamber, ensuring oxidation-free results.
4. Proper Mold Preparation: Ensuring molds are dry and free from contaminants reduces the risk of oxidation reactions during pouring.
5. Controlled Cooling Rates: Gradual cooling prevents rapid oxidation by reducing thermal stress on the metal surface.
By implementing these strategies, manufacturers can produce high-quality castings with minimal oxidation-related defects, enhancing durability and performance.