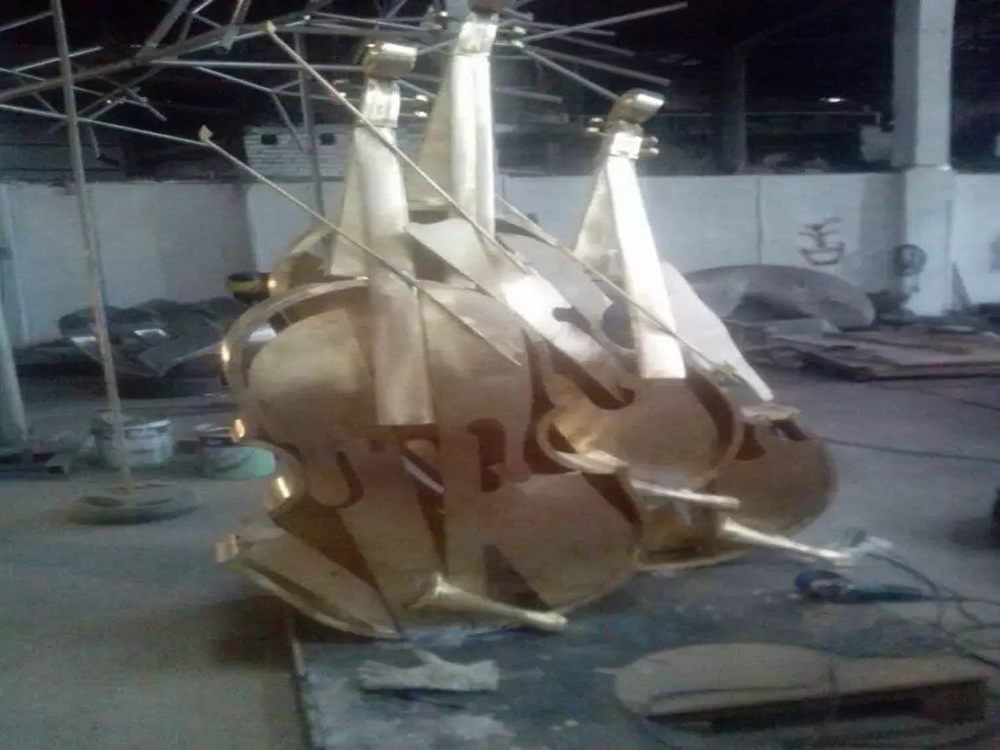
Welding serves as the invisible backbone of multi-piece bronze sculpture creation, transforming separate cast elements into unified artistic masterpieces. Unlike industrial welding, sculptural welding demands exceptional precision and artistry to maintain aesthetic integrity while ensuring structural soundness.
Artists employ specialized techniques like TIG (Tungsten Inert Gas) welding for its clean, controllable heat that minimizes bronze discoloration. The process begins with meticulous alignment of pre-cast sections, often using temporary fixtures. Welders then carefully fuse joints with bronze filler rods matching the sculpture's alloy composition, creating nearly invisible seams.
Beyond mere assembly, welding enables sculptors to achieve impossible single-cast designs - from delicate outstretched limbs to complex abstract forms. It also allows for repairs and modifications during creation. Modern sculptors sometimes intentionally highlight welds as design elements, celebrating the fabrication process.
The welding process affects the sculpture's longevity. Properly executed welds prevent stress fractures and withstand outdoor elements when the artwork is installed. Contemporary conservation methods even use welding for restoring ancient bronze artworks, proving its enduring importance in metal sculpture preservation.