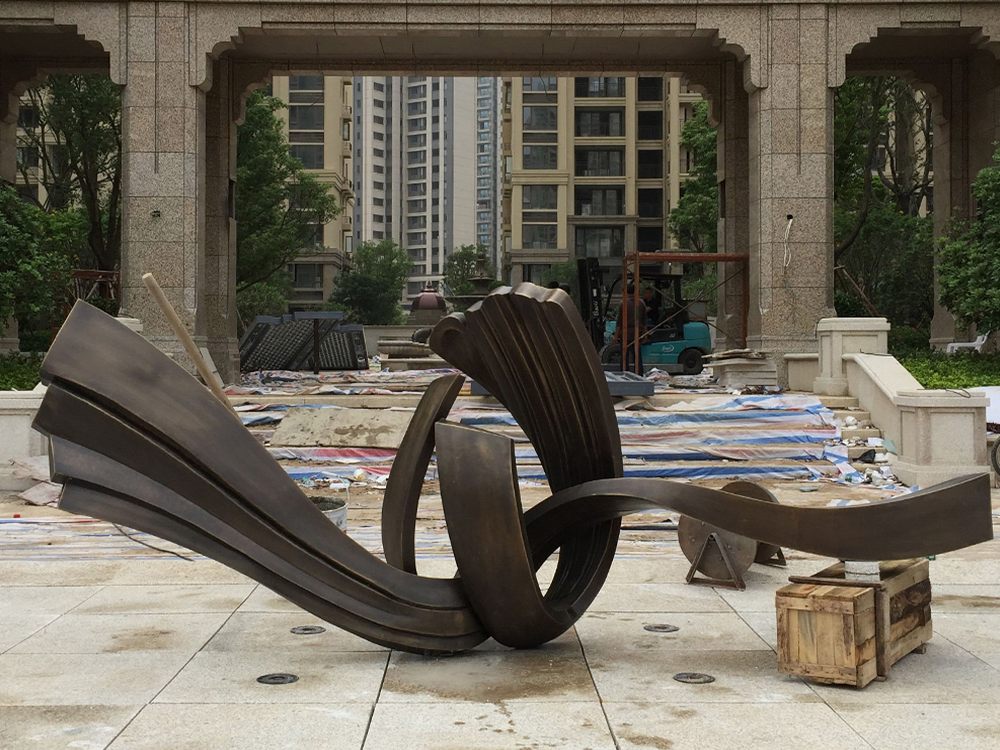
Creating bronze sculptures with ultra-thin sections presents a unique set of challenges that test the limits of both artistic vision and technical craftsmanship. One of the primary difficulties lies in the casting process. Bronze, a metal alloy primarily composed of copper and tin, requires precise temperature control during pouring. Ultra-thin sections cool faster than thicker parts, leading to potential cracks or incomplete fills, which can compromise the sculpture's structural integrity.
Another significant challenge is maintaining the sculpture's durability. Thin bronze sections are more prone to bending or warping over time, especially in outdoor installations exposed to weather conditions. Artists must carefully balance aesthetic delicacy with material strength, often reinforcing thin areas with internal supports or adjusting the alloy composition for added resilience.
The finishing process also becomes more demanding. Polishing and patinating ultra-thin sections require exceptional skill to avoid damaging the delicate metal. Each stroke of the tool carries greater risk, as thin bronze can easily deform under pressure.
Despite these challenges, many artists pursue ultra-thin bronze work for its breathtaking visual effect—creating the illusion of weightlessness in a traditionally heavy medium. Mastering this technique represents a pinnacle of metalworking artistry, blending centuries-old foundry techniques with modern innovation.