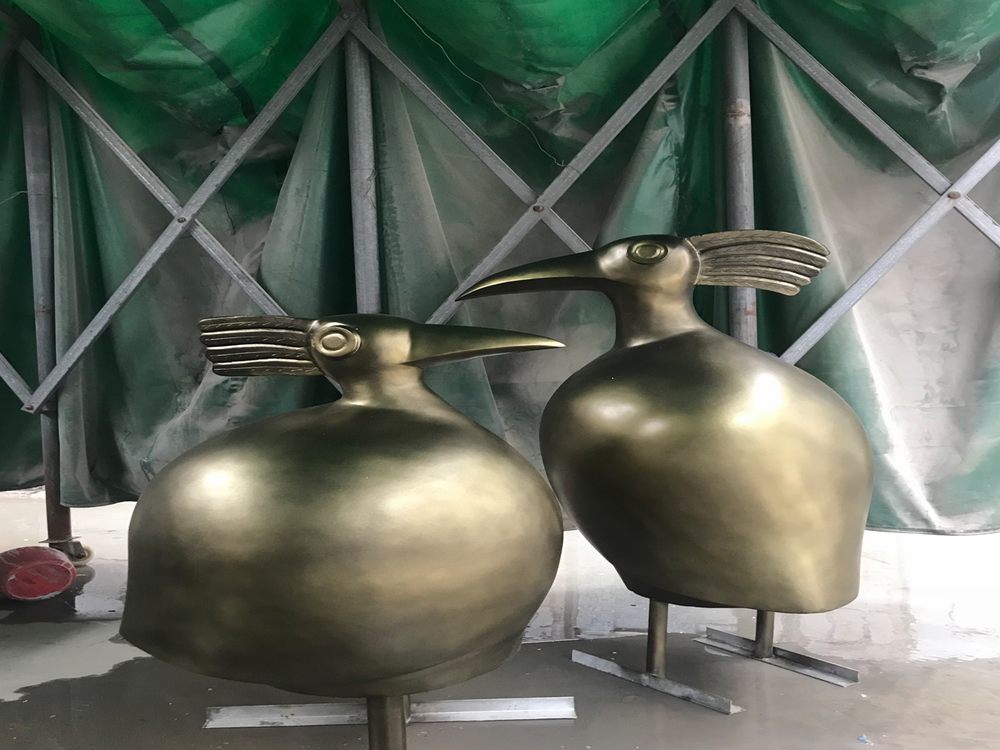
Bronze casting is a timeless art form that has been used for centuries to create intricate sculptures and functional objects. Two primary methods dominate this craft: direct and indirect bronze casting. Understanding their differences is essential for artists, craftsmen, and enthusiasts alike.
Direct Bronze Casting involves pouring molten bronze directly into a mold created from the original model, often made of wax or clay. This method is favored for its simplicity and ability to capture fine details. The mold is typically destroyed during the process, making each piece unique. Direct casting is ideal for one-of-a-kind sculptures or small production runs.
Indirect Bronze Casting, on the other hand, uses an intermediary mold, often made of rubber or silicone, to create a reusable master mold. This allows for multiple reproductions of the same design without damaging the original model. Indirect casting is more cost-effective for large-scale production but may sacrifice some detail compared to direct methods.
Key differences include:
1. Mold Durability: Direct casting molds are single-use, while indirect molds can be reused.
2. Detail Preservation: Direct casting often achieves higher detail fidelity.
3. Production Scale: Indirect casting is better suited for mass production.
4. Cost Efficiency: Indirect casting reduces costs for repeated pieces.
Both methods have their place in bronze casting, with the choice depending on the project's requirements, budget, and desired outcome. Whether creating a unique sculpture or a series of identical pieces, understanding these techniques ensures the best results.