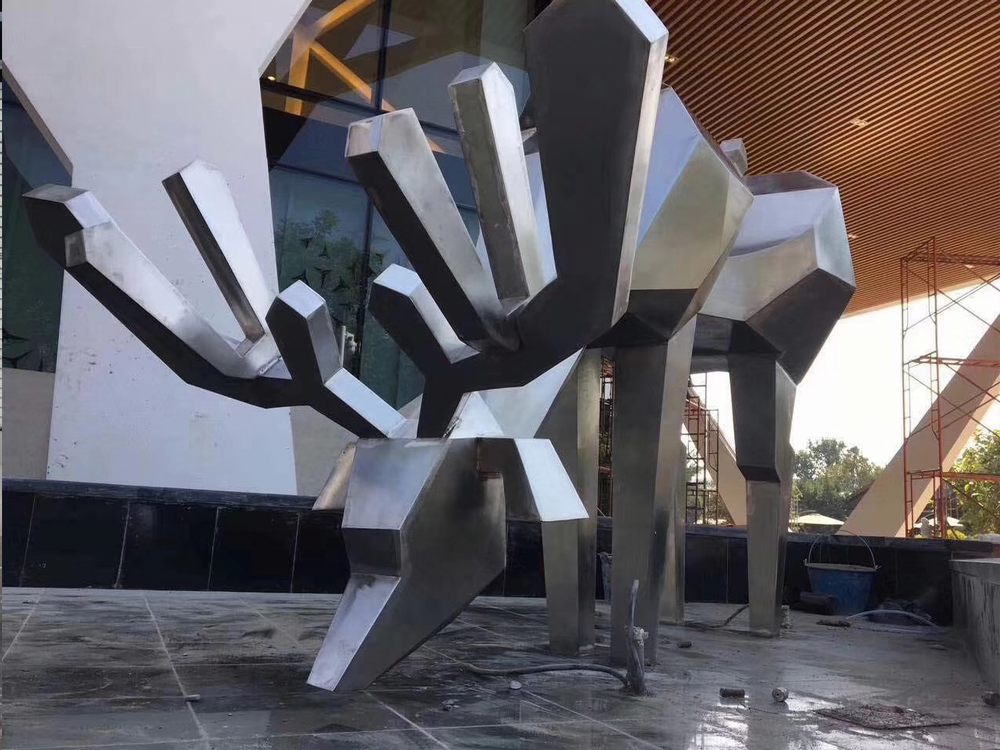
Collaborating with foundries on custom bronze sculptures requires a blend of artistic vision and technical precision. To ensure a successful partnership, follow these best practices:
1. Clear Design Communication: Provide detailed sketches, 3D models, or maquettes to the foundry. This minimizes misunderstandings and ensures your vision is accurately translated into metal.
2. Material and Process Knowledge: Understand bronze alloys, patina options, and casting techniques (e.g., lost-wax or sand casting). Discuss these with the foundry to align expectations.
3. Timeline and Budget Transparency: Establish realistic deadlines and cost estimates early. Bronze casting involves multiple stages—mold-making, casting, chasing, and patination—each impacting time and budget.
4. Regular Site Visits: If possible, visit the foundry during key phases (e.g., wax inspection, metal pouring). This allows for adjustments and fosters trust.
5. Finishing and Patina Collaboration: Work closely with the foundry’s artisans to select patinas and finishes. Samples or test pieces can help finalize the desired aesthetic.
By fostering open communication and mutual respect, artists and foundries can create stunning, enduring bronze sculptures that reflect both craftsmanship and creativity.