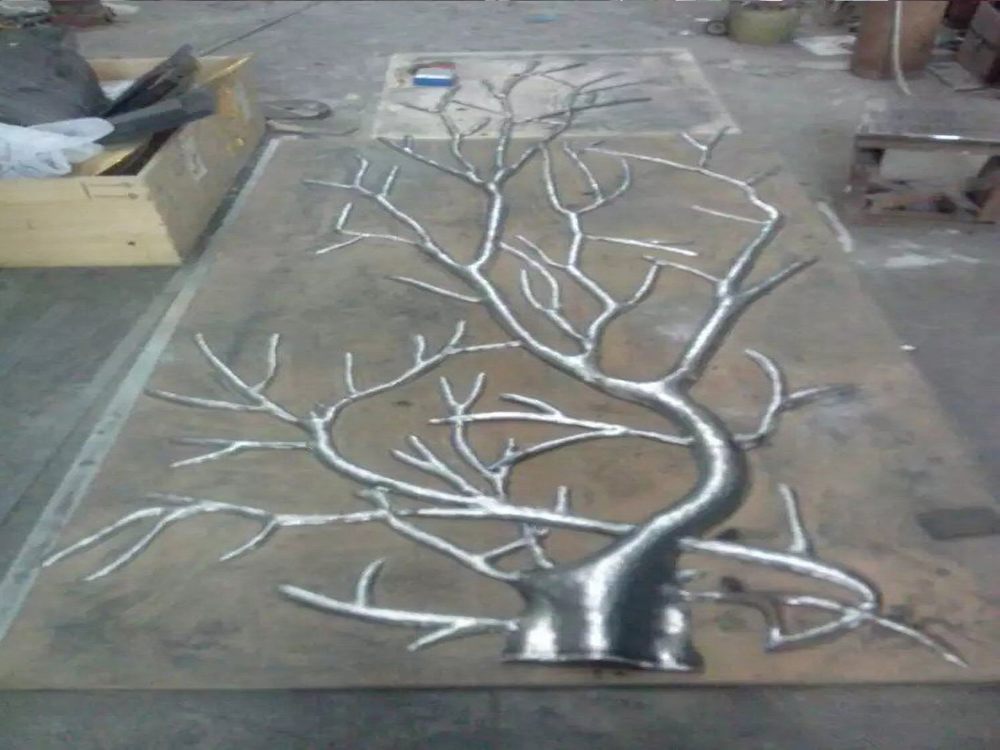
Creating modular bronze sculptures for flexible installations requires a blend of artistic vision and technical precision. Here are the best practices to ensure success:
1. Design for Modularity: Plan each module to be self-contained yet easily connectable. Use standardized joints or interlocking mechanisms to allow for reconfiguration. Sketch detailed blueprints to visualize how pieces will fit together in various arrangements.
2. Material Selection: Bronze is ideal for its durability and malleability, but consider alloy variations for specific needs. Opt for lighter bronze alloys if portability is a priority, or patina finishes to enhance visual appeal.
3. Precision Casting: Employ lost-wax casting or 3D printing for accurate module replication. Ensure each piece is flawlessly cast to avoid fitting issues during assembly.
4. Flexible Joining Systems: Incorporate hidden bolts, magnetic connectors, or slot-and-tab systems for seamless modular assembly. Test these systems rigorously to ensure stability in different configurations.
5. Surface Treatment: Apply consistent patinas or textures across modules to maintain cohesion, even when rearranged. Experiment with finishes that adapt to different lighting conditions.
6. Installation Adaptability: Design modules to function as standalone pieces or part of larger installations. Consider weight distribution and structural support for varied display environments.
By following these practices, artists can create versatile bronze sculptures that adapt to diverse spaces while maintaining artistic integrity. Modularity opens endless possibilities for dynamic, evolving art installations.