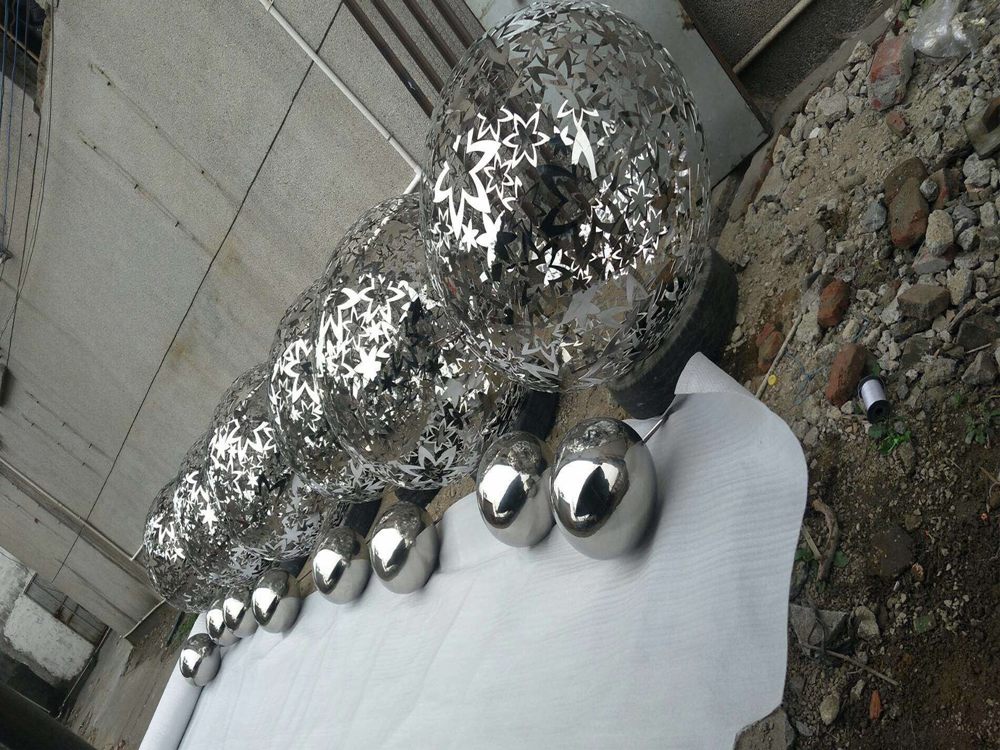
Bronze alloys have been used for millennia, but modern advancements have introduced experimental compositions that differ significantly from traditional formulas. Traditional bronze typically consists of copper and tin, often with trace elements like lead or zinc, offering durability and corrosion resistance for sculptures, tools, and musical instruments.
Experimental bronze alloys, however, incorporate unconventional elements such as aluminum, silicon, or even rare earth metals to enhance specific properties. These innovations can improve tensile strength, thermal conductivity, or resistance to wear, making them suitable for aerospace, electronics, and high-performance engineering applications.
Another key difference lies in production techniques. Traditional bronze relies on time-tested casting methods, while experimental alloys often employ advanced metallurgical processes like rapid solidification or powder metallurgy. This allows for finer grain structures and tailored material characteristics.
Cost and availability also separate the two. Traditional bronze remains more accessible and cost-effective for general use, whereas experimental variants often require specialized manufacturing and rare materials, limiting their adoption to niche industries.
Ultimately, the choice between traditional and experimental bronze depends on the application's demands, balancing historical reliability against cutting-edge performance.