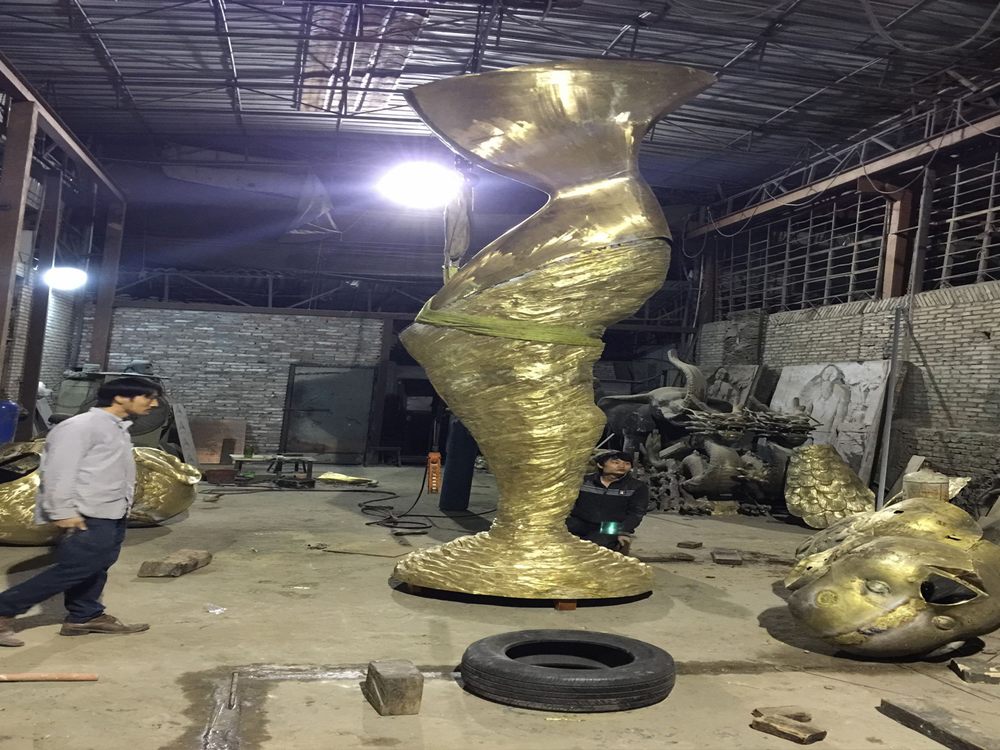
Creating bronze sculptures with intricate details while ensuring structural integrity is a delicate balance mastered by skilled artists through centuries-old techniques and modern innovations. The process begins with meticulous planning, where artists design the sculpture with both aesthetics and durability in mind.
One of the most common methods is the lost wax casting technique, which allows for exceptional precision. Artists first sculpt the design in wax, capturing every minute detail. This wax model is then encased in a ceramic mold. When heated, the wax melts away, leaving a cavity that perfectly mirrors the original design. Molten bronze is poured into this cavity, solidifying into a detailed replica of the wax model.
To maintain structural integrity, artists often employ strategic reinforcements. Internal armatures or thicker sections in high-stress areas prevent cracking or warping. Additionally, alloys with optimal strength-to-ductility ratios, such as silicon bronze, are favored for their ability to hold fine details without brittleness.
Post-casting, artisans use chasing and patination to refine details further. Chasing involves hand-tooling the bronze to sharpen lines and textures, while patination adds depth through chemical treatments. These finishing touches enhance the sculpture’s visual complexity without compromising its durability.
Through a combination of traditional craftsmanship and material science, artists achieve breathtaking detail in bronze sculptures that stand the test of time.