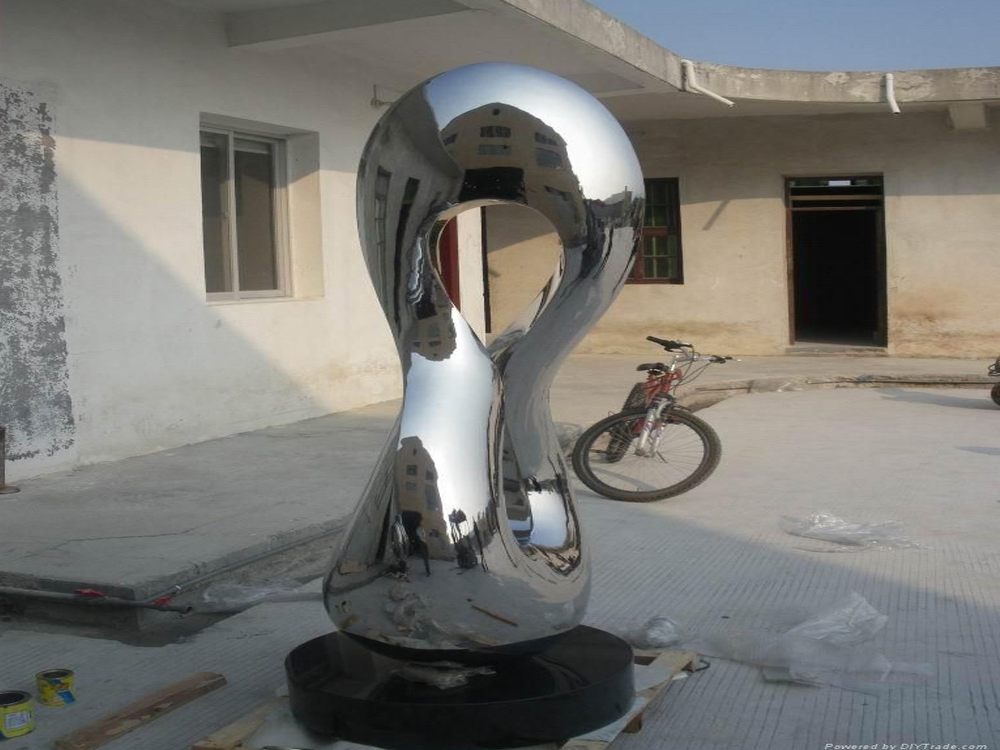
Bronze alloys have been used for centuries, but modern metallurgy has introduced experimental variations with distinct properties. Traditional bronze alloys typically consist of copper and tin, often with small additions of lead or zinc. These alloys are prized for their durability, corrosion resistance, and historical significance in art and engineering.
Experimental bronze alloys, however, incorporate unconventional elements like aluminum, silicon, or nickel to enhance specific characteristics. These modern blends may offer improved strength-to-weight ratios, better thermal conductivity, or unique aesthetic finishes. For instance, aluminum bronze exhibits superior wear resistance, making it ideal for heavy-duty applications.
Another key difference lies in their microstructure. Traditional bronzes often have a more predictable grain structure, while experimental alloys may feature engineered phases for tailored performance. Additionally, experimental bronzes frequently undergo advanced processing techniques like rapid solidification or powder metallurgy to achieve refined properties.
Cost and availability also vary significantly. Traditional bronzes benefit from established supply chains, whereas experimental alloys may involve rare or expensive additives. Despite this, the push for innovation in aerospace, electronics, and renewable energy continues to drive the development of novel bronze compositions.
Ultimately, the choice between traditional and experimental bronze depends on the application's demands, balancing historical reliability against cutting-edge performance.