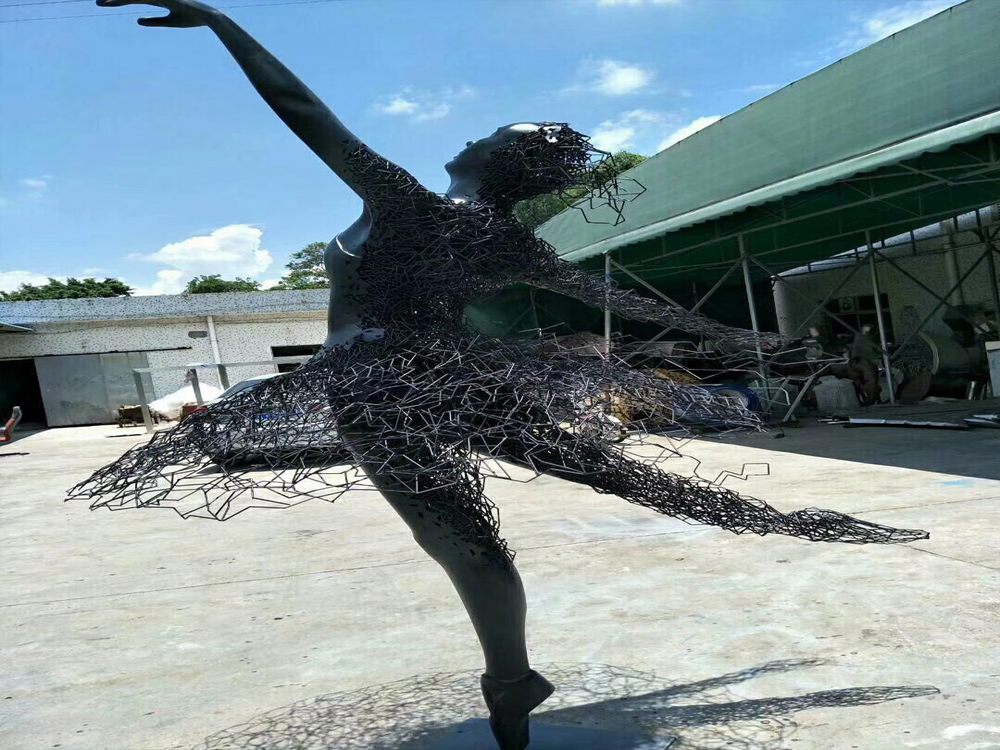
Bronze welding has evolved significantly over time, with traditional and contemporary methods offering distinct advantages. Traditional bronze welding often relied on forge welding or brazing techniques, requiring skilled artisans to heat and hammer bronze pieces together. These methods emphasized manual craftsmanship but were limited in precision and repeatability.
Contemporary bronze welding, on the other hand, incorporates advanced technologies like TIG (Tungsten Inert Gas) welding and laser welding. These methods provide greater control over heat input, reducing distortion and improving joint strength. Modern techniques also allow for the use of specialized filler metals and fluxes, enhancing corrosion resistance and aesthetic appeal.
Another key difference lies in efficiency. Traditional methods were time-consuming and labor-intensive, while contemporary welding enables faster production with consistent results. Additionally, modern welding equipment offers improved safety features, reducing risks associated with fumes and high temperatures.
Both approaches have their place—traditional methods preserve historical authenticity in restoration projects, while contemporary techniques dominate industrial applications. Understanding these differences helps craftsmen and engineers choose the right method for their specific bronze welding needs.