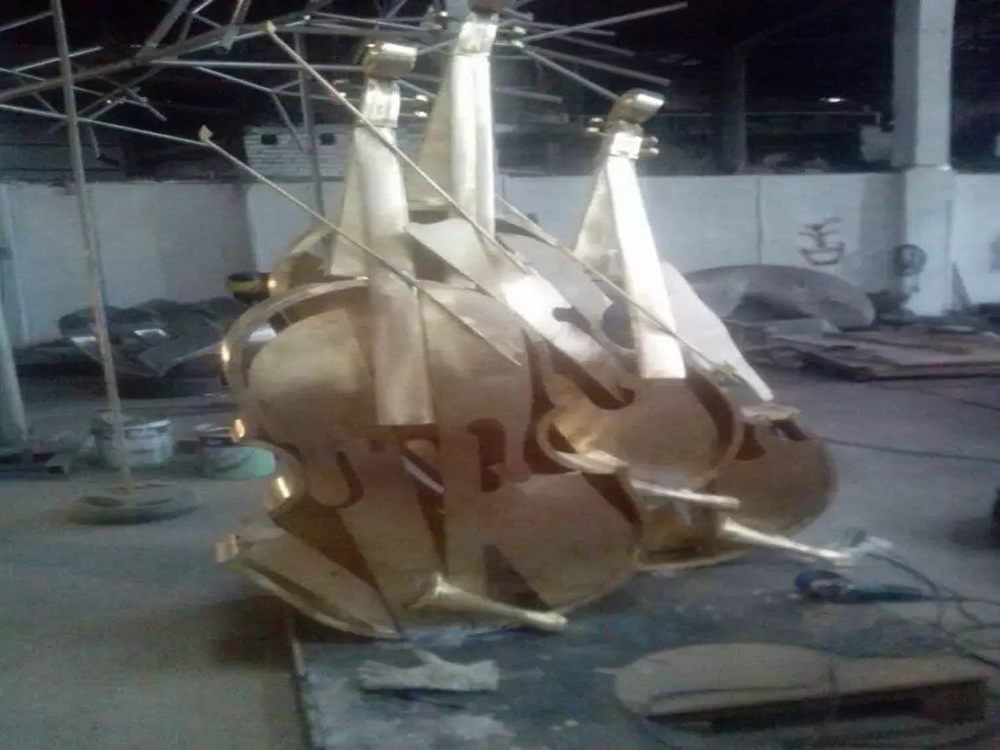
The durability of a bronze sculpture is heavily influenced by its alloy composition, which determines its resistance to corrosion, mechanical strength, and overall longevity. Traditional bronze consists primarily of copper and tin, but varying the proportions of these metals—or adding elements like zinc, lead, or phosphorus—can significantly alter the sculpture's properties.
Higher tin content increases hardness and casting quality but may make the metal more brittle. Conversely, adding zinc creates a more malleable alloy, while lead improves machinability at the cost of structural integrity. Modern alloys may incorporate aluminum or silicon for enhanced corrosion resistance, particularly in outdoor sculptures exposed to weathering.
Environmental factors also interact with alloy composition—certain mixtures resist patina formation better, while others develop a desirable protective layer over time. Artists and foundries must balance aesthetic goals with practical durability when selecting an alloy, ensuring the sculpture withstands both time and environmental stresses. The right composition preserves fine details while maintaining structural stability for centuries, making bronze one of the most enduring mediums in art history.