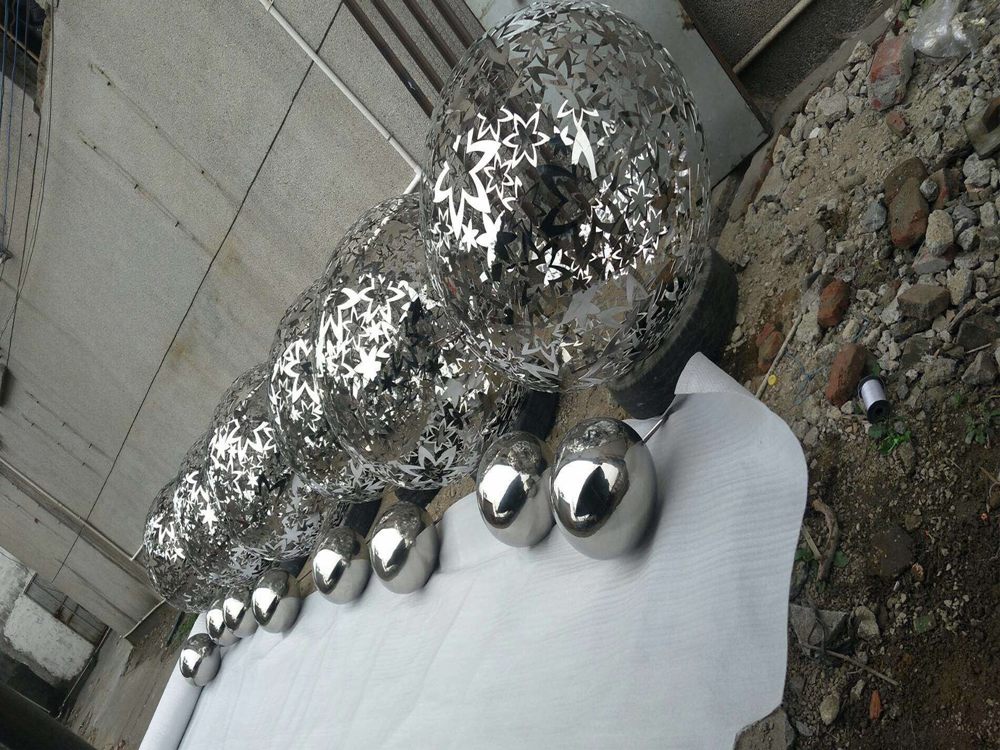
Bronze casting is a complex process that can be prone to various defects if not executed properly. The most common issues include porosity, shrinkage cavities, misruns, cold shuts, and inclusions.
Porosity occurs when gas becomes trapped in the metal during solidification, creating small holes. This can be prevented by proper mold venting and controlling pouring temperature. Shrinkage cavities form when insufficient molten metal feeds into areas as the casting cools. Adequate risers and proper gating system design help avoid this problem.
Misruns and cold shuts happen when the metal cools too quickly before completely filling the mold. Maintaining proper pouring temperatures and ensuring adequate metal fluidity are key prevention methods. Inclusions result from foreign materials entering the molten metal, which can be minimized through proper filtering and clean handling practices.
Other defects like hot tears (cracks from uneven cooling) can be prevented by designing uniform wall thickness and controlling cooling rates. Surface defects such as scabs or metal penetration are avoided through proper mold material selection and coating.
Quality control measures including X-ray inspection, ultrasonic testing, and visual examination help identify these defects early. By understanding these common issues and implementing proper foundry techniques, manufacturers can significantly improve bronze casting quality and reduce waste.
Modern foundries combine traditional knowledge with computer simulations to predict and prevent potential defects before production begins, ensuring higher success rates in bronze casting projects.