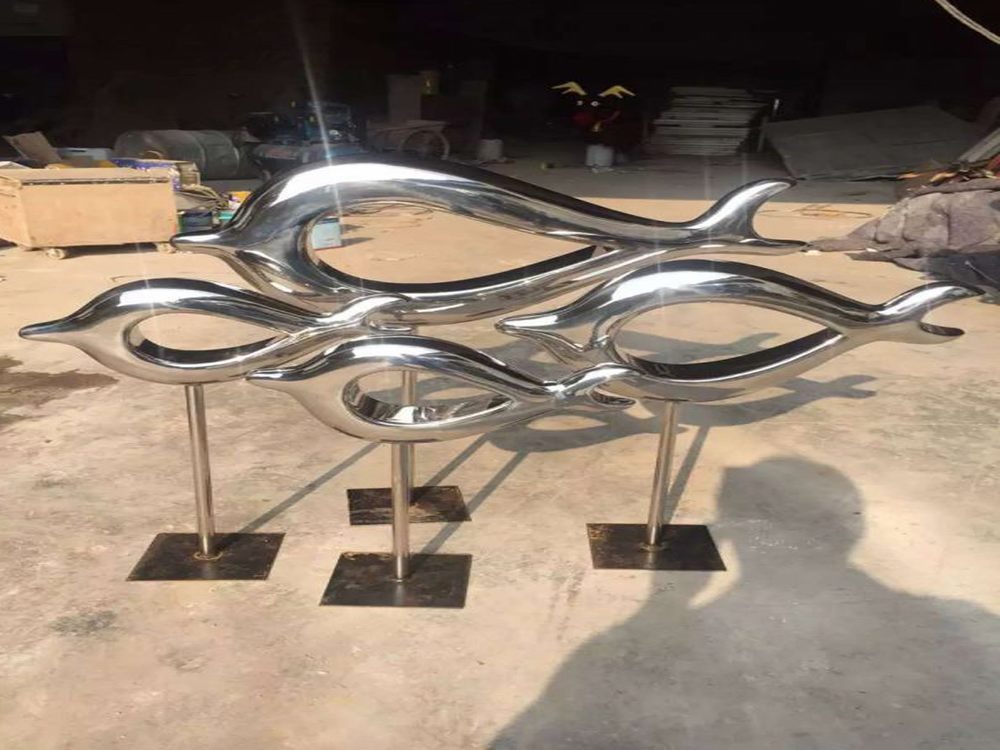
Creating ultra-thin bronze elements in sculptures presents a unique set of challenges that test the limits of both artistry and craftsmanship. One primary difficulty lies in the material itself—bronze, while durable, has limited malleability when forged into delicate, thin sections. Achieving consistent thickness without warping or cracking requires precise temperature control during casting and annealing.
Another hurdle is structural integrity. Ultra-thin bronze components are prone to bending or breaking under their own weight or external forces, demanding innovative support systems or alloy adjustments. Artists often experiment with bronze alloys or composite techniques to enhance strength while maintaining aesthetic finesse.
The casting process also becomes exponentially harder with thinner designs. Molten bronze must flow evenly into intricate molds, yet thin walls cool rapidly, risking incomplete fills or air bubbles. Advanced techniques like lost-wax casting or 3D-printed molds are employed to mitigate these issues.
Finally, finishing ultra-thin bronze demands exceptional skill. Polishing or patinating such fragile surfaces without causing damage requires specialized tools and a steady hand. Despite these challenges, the ethereal beauty of thin bronze elements continues to inspire sculptors to push the boundaries of metal artistry.