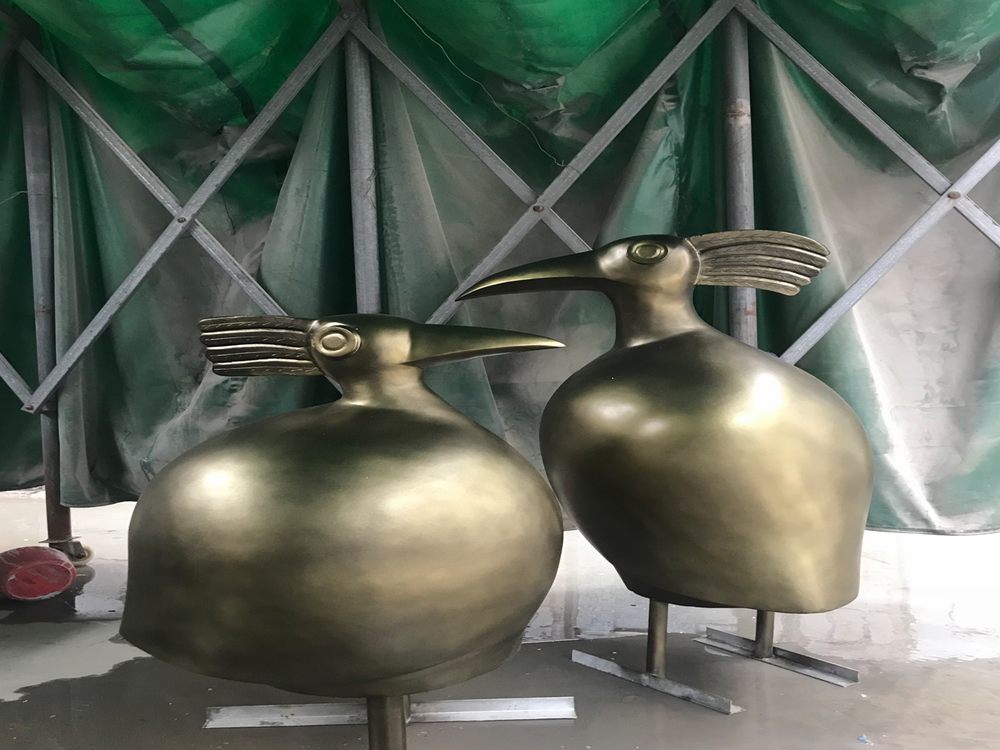
Creating bronze sculptures with impeccable proportion and scale is a meticulous process that blends artistry, mathematics, and craftsmanship. Artists begin by conceptualizing their design, often using sketches or small clay maquettes to visualize the final piece. The key to achieving accurate proportions lies in careful measurement—many sculptors employ calipers or proportional dividers to translate dimensions from reference models to the full-scale work.
For larger sculptures, artists frequently use the "grid method," dividing both the model and the final sculpture into corresponding sections to maintain consistency. Armatures—metal frameworks—provide structural support, ensuring stability as clay or wax is built up. The human figure, a common subject, demands particular attention to anatomical ratios; experienced sculptors often reference canonical systems like the "8-heads tall" rule for idealized figures.
The scaling process intensifies during the bronze casting phase. Traditional lost-wax casting requires creating a wax positive from the original model, which must perfectly preserve all proportions before being encased in ceramic mold. Any distortion at this stage would carry through to the final bronze pour. Modern techniques sometimes incorporate 3D scanning and printing to assist in scaling up smaller models with digital precision.
Finishing touches—chasing, patination, and polishing—can optically alter perceived scale. Darker patinas may make elements recede visually, while polished highlights can bring features forward. Master sculptors understand these optical effects and adjust their work accordingly, proving that proportion and scale in bronze sculpture are as much about perception as they are about precise measurement.