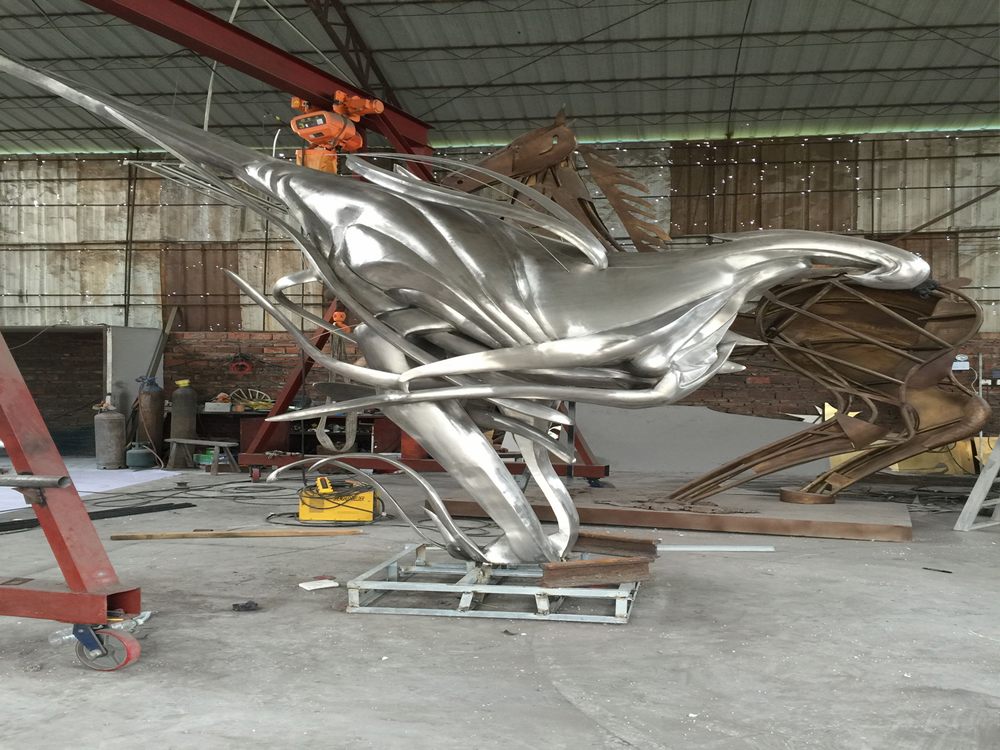
Creating bronze sculptures with intricate surface patterns presents a unique set of challenges for artists and sculptors. One of the primary difficulties lies in the casting process itself. Bronze, while durable, requires precise temperature control during pouring to avoid imperfections that could obscure delicate patterns. Even minor air bubbles or uneven cooling can ruin finely detailed designs.
Another significant hurdle is the initial modeling phase. Artists must carefully plan and execute the original pattern in clay or wax, knowing that every imperfection will be magnified in the final bronze piece. The translation from soft modeling material to hard metal often reveals unexpected flaws in the design.
Surface finishing poses its own complications. Intricate patterns make polishing and patina application particularly challenging, as different areas may require varying techniques. Deep recesses might collect excess patina while raised details could wear too quickly.
Tool access becomes problematic with complex geometries. Traditional sculpting tools may not reach all areas of an elaborate design, forcing artists to develop custom tools or modify their techniques. This limitation often leads to compromises in the original artistic vision.
Finally, the weight distribution of sculptures with uneven surface patterns requires careful engineering. Heavy ornamentation on one side can create structural weaknesses, demanding additional internal supports that might interfere with the artwork's aesthetic.
Mastering these challenges requires not only artistic skill but also deep technical knowledge of metallurgy and casting processes, making such sculptures true testaments to an artist's craftsmanship.