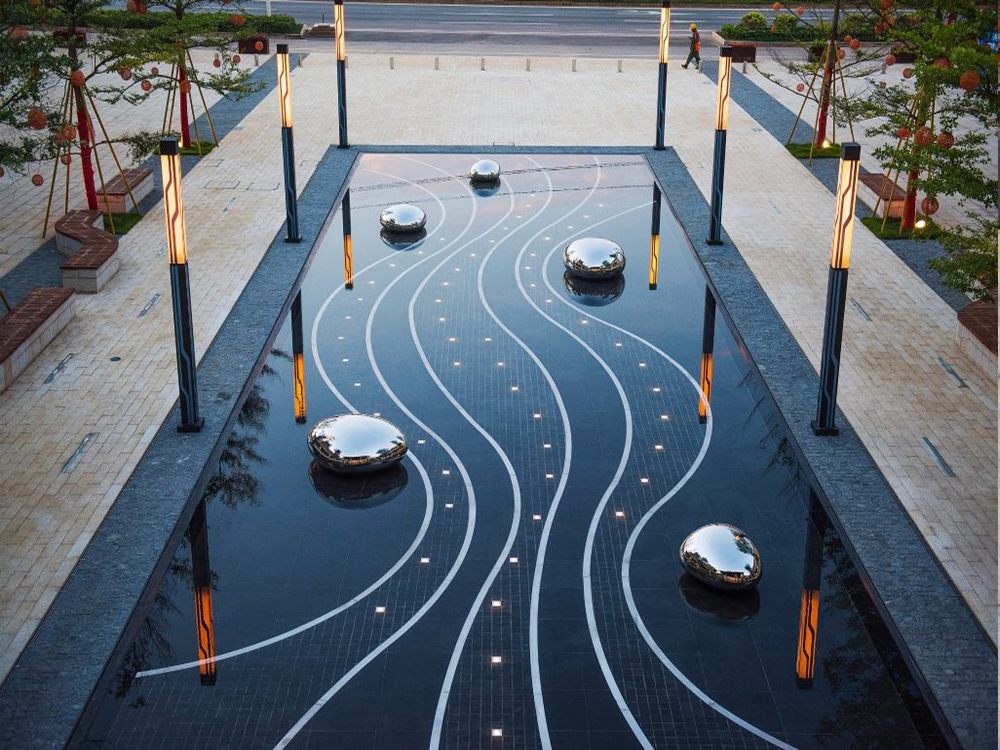
Bronze casting is a revered ancient technique, but it is not without its challenges. Several common defects can arise during the process, affecting the quality and durability of the final product.
1. Porosity: One of the most frequent issues, porosity occurs when gas bubbles become trapped in the metal as it solidifies. This weakens the structure and can lead to cracks. Mitigation involves proper mold venting, controlled pouring temperatures, and degassing the molten bronze before casting.
2. Shrinkage Cavities: As bronze cools, it contracts, sometimes leaving voids or cavities. To minimize this, foundries use risers or feeders to supply additional molten metal to compensate for shrinkage.
3. Cold Shuts: These occur when two streams of molten metal fail to fuse properly, creating weak seams. Ensuring adequate pouring speed and maintaining optimal metal temperature can prevent this defect.
4. Inclusions: Foreign particles like slag or oxides can become embedded in the casting. Skimming the molten metal and using clean, high-quality materials reduce the risk.
5. Misruns: Incomplete filling of the mold results in misruns. Proper gating design and preheating molds help ensure complete cavity filling.
By understanding these defects and implementing corrective measures, artisans and foundries can produce high-quality bronze castings with fewer flaws. Advanced techniques like X-ray inspection and pressure testing further enhance defect detection and resolution.
Mastering these mitigation strategies ensures that bronze casting remains both an art and a precision craft.