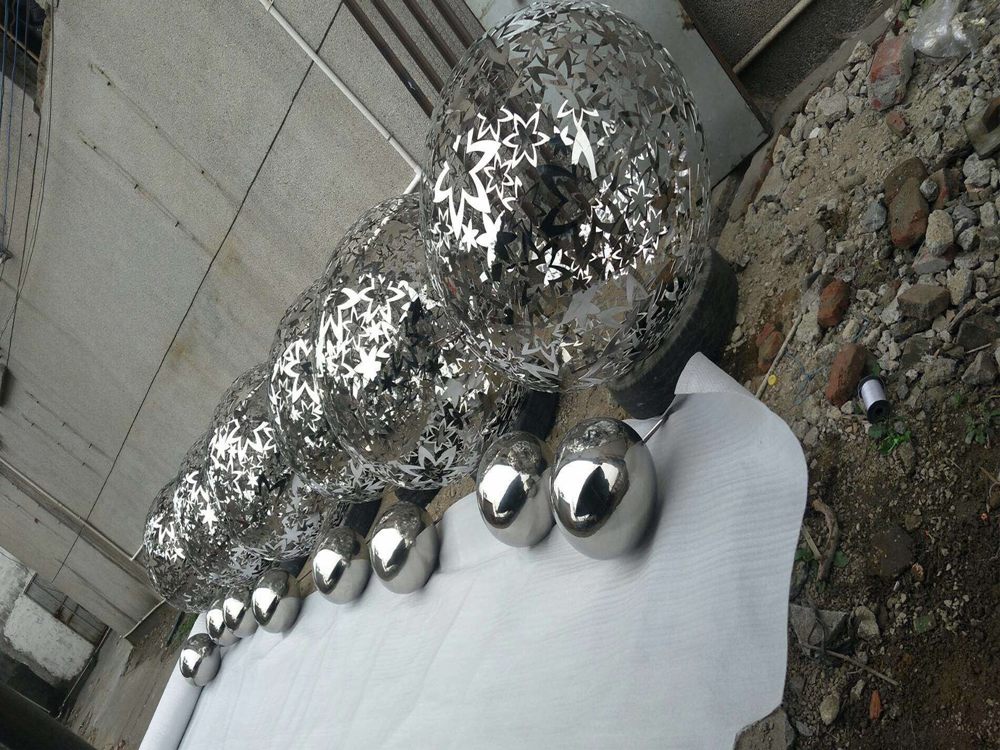
Bronze sculpture production, while celebrated for its artistic and cultural value, carries significant environmental consequences often overlooked in the art world. The process begins with resource extraction - mining copper and tin (bronze's primary components) disrupts ecosystems through deforestation, soil erosion, and water contamination. Energy-intensive smelting processes release sulfur dioxide and particulate matter, contributing to air pollution and acid rain.
Traditional lost-wax casting methods consume substantial amounts of water and generate hazardous waste, including used investment molds containing silica dust. The foundry phase produces greenhouse gases through fossil fuel combustion in furnaces reaching 2,100°F (1,150°C). Chemical patination processes often involve toxic compounds like ferric nitrate and liver of sulfur that can leach into waterways.
A single life-sized bronze sculpture may generate 500-800 kg of CO2 equivalents, comparable to a transatlantic flight. The art sector is gradually addressing these impacts through recycled bronze (up to 90% less energy than virgin material), electric furnaces, and biodegradable mold alternatives. Some contemporary artists now incorporate these concerns into their work, using bronze's longevity (potentially 5,000+ years) as an argument for creating fewer, more meaningful pieces.
While bronze remains irreplaceable for certain artistic expressions, understanding its environmental footprint allows for more informed material choices and sustainable practices in sculpture production. Emerging techniques like 3D-printed sand molds and closed-loop water systems demonstrate how tradition can evolve with ecological awareness.