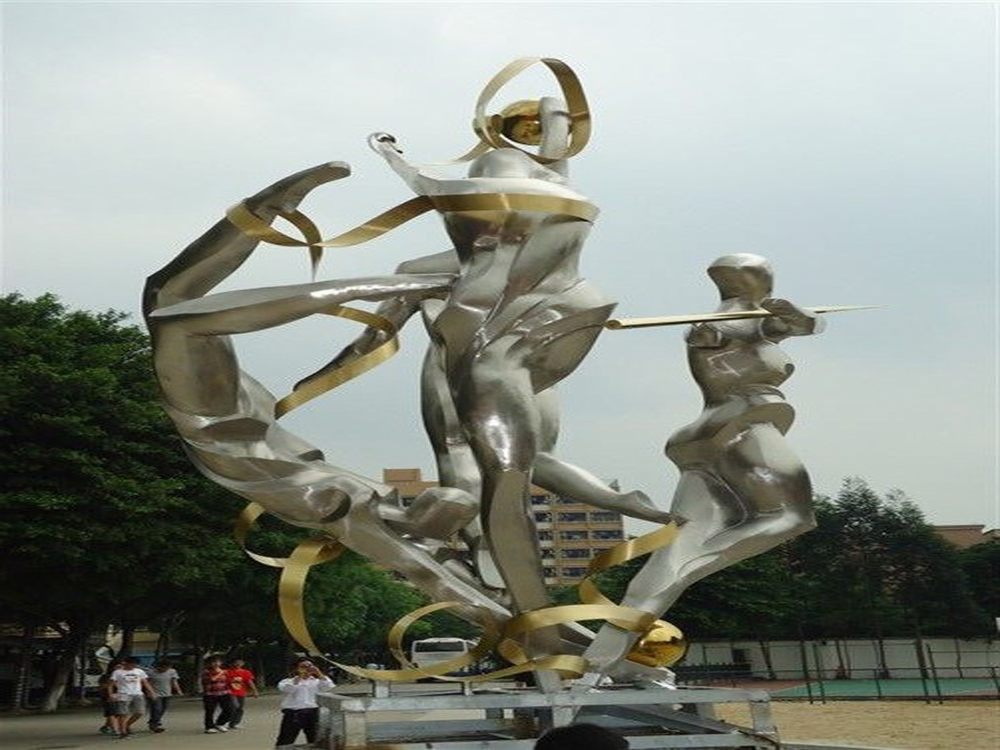
Bronze casting is a revered art form with two primary methods: studio casting and foundry casting. While both techniques produce stunning bronze artworks, they differ significantly in scale, process, and artistic control.
Studio casting is typically performed by individual artists or small workshops, allowing for greater creative freedom and hands-on involvement. This method often employs simpler equipment like ceramic shell or lost-wax techniques, making it ideal for limited editions or unique pieces. Artists maintain direct oversight of every step, from mold-making to finishing touches.
Foundry casting, by contrast, operates on an industrial scale with specialized machinery and teams of technicians. Large foundries handle high-volume production, using sand casting or centrifugal casting for efficiency. While offering precision and consistency, this approach may limit artistic customization due to standardized processes.
Key differences include:
1. Control: Studio casting offers personalized artistry; foundries prioritize reproducibility.
2. Scale: Studios create singular works; foundries excel at mass production.
3. Equipment: Studios use manual tools; foundries employ industrial furnaces and automation.
4. Finish: Studio pieces often show hand-worked textures; foundry works have machine-polished surfaces.
Artists choose based on project needs – studios for bespoke creations, foundries for architectural or commercial applications. Both methods preserve bronze's timeless beauty through distinct approaches to this ancient craft.