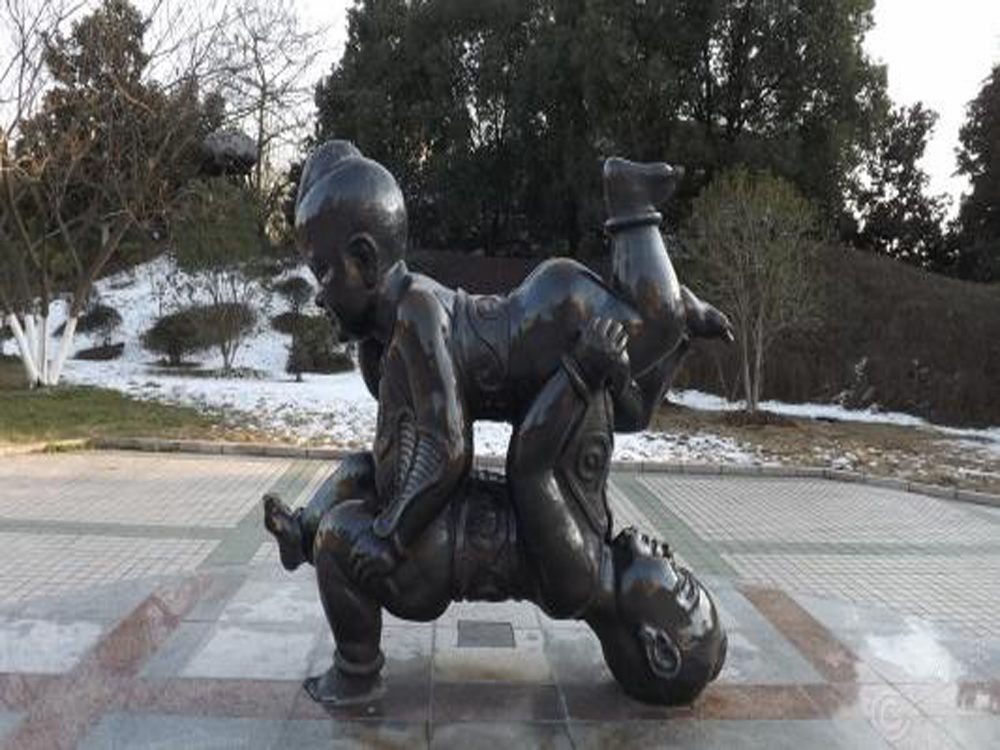
Creating bronze sculptures with intricate undercuts or negative spaces is a testament to an artist's skill and patience. The process often begins with the lost wax casting method, a centuries-old technique that allows for exceptional detail. Artists first sculpt their design in wax, carefully carving out undercuts and negative spaces to achieve the desired complexity. The wax model is then coated in a ceramic shell, which hardens to form a mold. Once the wax is melted away, molten bronze is poured into the mold, filling every crevice. After cooling, the ceramic shell is broken away, revealing the raw bronze sculpture.
To refine undercuts and negative spaces, artists employ specialized tools like chisels, files, and pneumatic grinders. These tools help smooth rough edges and enhance fine details that may have been obscured during casting. For particularly delicate areas, artists might use a technique called "chasing," where they manually hammer and texture the bronze to perfect its form.
Another innovative approach involves 3D printing, where artists design the sculpture digitally and print a wax model layer by layer. This method allows for even more intricate undercuts and negative spaces, as the precision of 3D printing surpasses traditional hand-carving in some cases.
Finally, the sculpture undergoes patination, where chemicals are applied to the bronze to create unique colors and textures. This step not only enhances the visual appeal but also protects the metal from corrosion. Through a combination of traditional craftsmanship and modern technology, artists continue to push the boundaries of bronze sculpture, creating breathtaking works that defy the limitations of the medium.