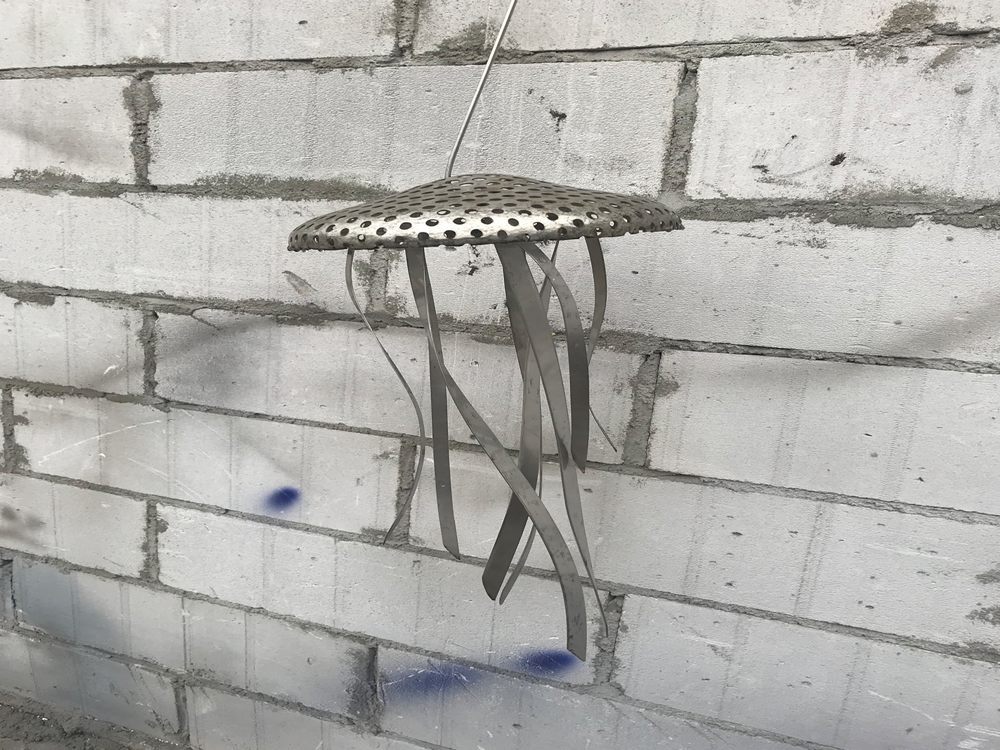
Welding bronze sculptures is a delicate art that requires precision and expertise. One of the most common challenges is controlling heat distribution, as bronze is highly conductive and prone to warping or cracking under excessive temperatures. Artists must carefully manage the welding torch to avoid damaging the sculpture's intricate details.
Another issue is material compatibility. Bronze alloys vary in composition, and using the wrong filler metal can lead to weak joints or discoloration. Selecting the correct welding rod is crucial for a seamless repair or assembly.
Finishing the welded area is equally challenging. Bronze develops a patina over time, and matching this natural oxidation after welding requires skillful polishing and chemical treatments. Additionally, the porosity of bronze can trap gases during welding, leading to bubbles or weak spots in the joint.
To overcome these challenges, experienced welders recommend using TIG welding for its precision, preheating the sculpture to reduce thermal stress, and practicing on scrap bronze before working on the final piece. Proper post-welding treatments, such as grinding and patination, ensure the repaired area blends seamlessly with the original artwork.
By understanding these common hurdles and adopting best practices, artists and restorers can achieve durable and aesthetically pleasing results in bronze sculpture welding.