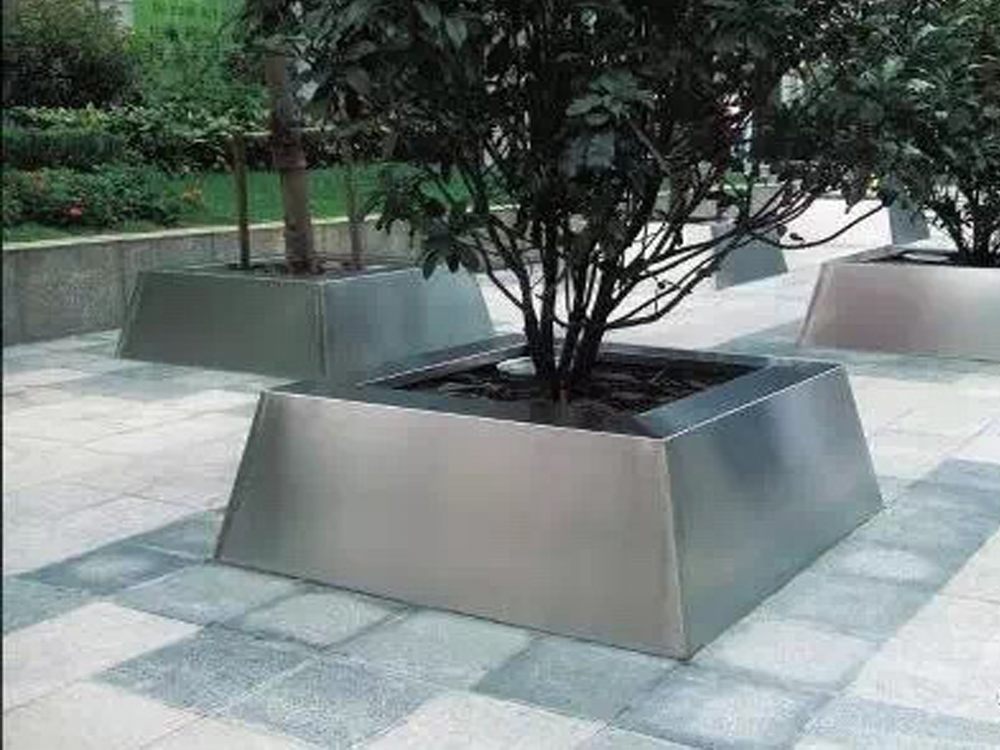
Gas porosity is a common challenge in bronze casting, where trapped gases create unwanted bubbles or voids in the final artwork. Artists employ several proven techniques to minimize this issue. First, proper mold preparation is critical—using well-vented molds and ensuring complete dryness prevents steam formation. Many foundries degas the molten bronze by introducing nitrogen or argon to purge dissolved gases.
Temperature control plays a vital role; maintaining optimal pouring temperatures (typically 1900-2100°F) allows gases to escape before solidification. Some artists use rotational casting to distribute material evenly while letting bubbles rise. Advanced practitioners often add small amounts of phosphorus as a deoxidizer to improve metal fluidity and gas release.
Post-casting, artists may employ X-ray inspection to detect internal porosity, allowing for careful repairs if needed. These combined methods help create durable, bubble-free bronze sculptures that stand the test of time.