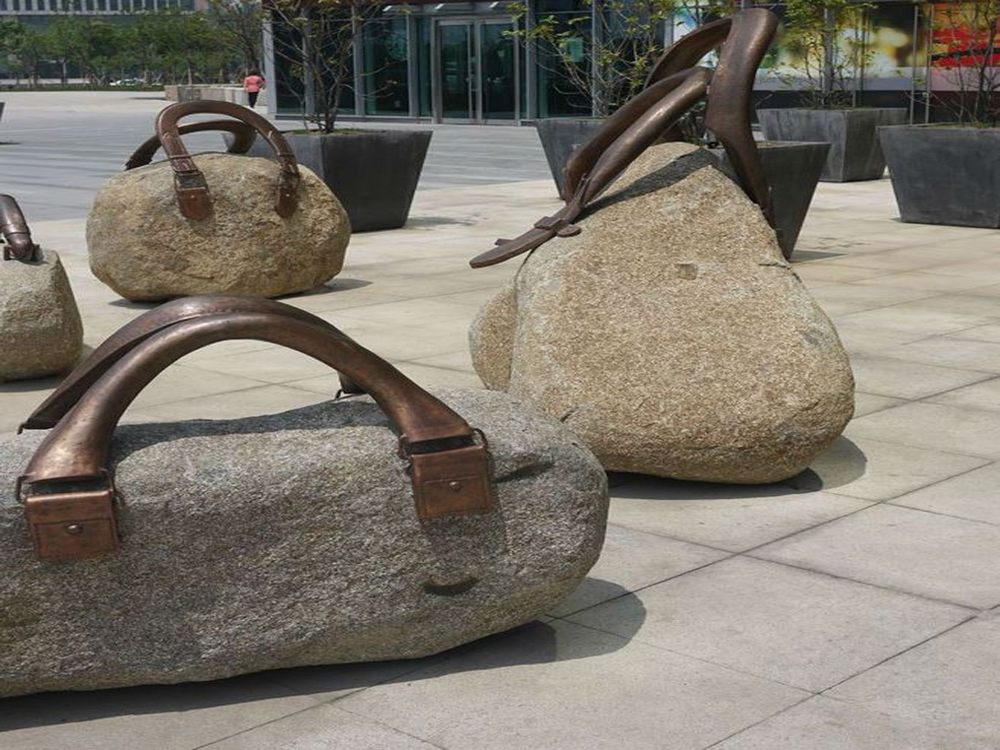
The lost-wax casting process, also known as investment casting, is a meticulous and ancient technique used to create intricate bronze sculptures. Here are the key steps involved:
1. Creating the Original Model: The process begins with an artist sculpting the original model, typically using clay or wax. This model captures every fine detail of the final sculpture.
2. Making the Wax Replica: A mold is created from the original model, and molten wax is poured into it to produce a wax replica. This replica is then refined to ensure precision.
3. Building the Ceramic Shell: The wax replica is coated with a ceramic slurry and silica sand, layer by layer, to form a heat-resistant shell. Once dried, the shell is heated to melt and drain the wax, leaving a hollow cavity.
4. Pouring Molten Bronze: The ceramic shell is preheated, and molten bronze is poured into the cavity. The bronze fills every detail of the mold, taking the shape of the original sculpture.
5. Breaking the Shell: After cooling, the ceramic shell is carefully broken away to reveal the rough bronze casting.
6. Finishing and Patina: The bronze sculpture is cleaned, polished, and any imperfections are removed. Finally, a patina is applied to achieve the desired color and finish, enhancing the artwork’s aesthetic appeal.
This time-honored method ensures that each bronze sculpture is a unique masterpiece, showcasing the artist’s vision and craftsmanship.