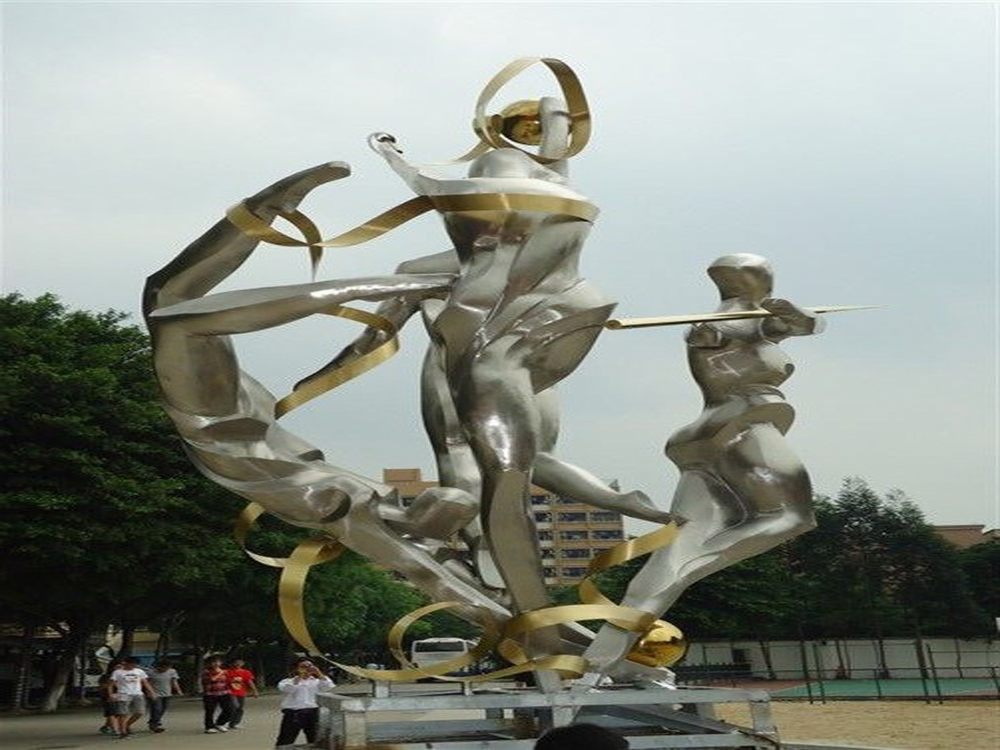
When selecting a casting method for bronze components, understanding the distinctions between investment casting and centrifugal casting is crucial. Both techniques offer unique advantages, but their processes and outcomes differ significantly.
Investment Casting (Lost-Wax Casting)
Investment casting is a precision-driven method ideal for intricate bronze parts. The process begins with a wax pattern coated in ceramic slurry, which hardens into a mold. After melting the wax, molten bronze fills the cavity, yielding high-detail components with smooth surfaces. This method excels in producing complex geometries, such as artistic sculptures or aerospace components, with minimal post-processing.
Centrifugal Casting
Centrifugal casting forces molten bronze into a spinning mold using centrifugal force. This technique suits cylindrical or symmetrical shapes like pipes, rings, or bushings. The rapid rotation ensures dense, bubble-free structures with superior mechanical properties. However, it lacks the fine-detail capability of investment casting and is better suited for simpler, rotation-friendly designs.
Key Differences
1. Precision: Investment casting achieves tighter tolerances (±0.005 inches) vs. centrifugal casting (±0.03 inches).
2. Shape Complexity: Investment supports intricate designs; centrifugal works best for axisymmetric parts.
3. Surface Finish: Investment-cast bronze requires less machining.
4. Production Scale: Centrifugal casting is faster for large batches of simple parts.
Choose investment casting for detailed, low-volume bronze items and centrifugal casting for high-strength, rotationally symmetric components. Each method’s cost-effectiveness depends on design requirements and production volume.