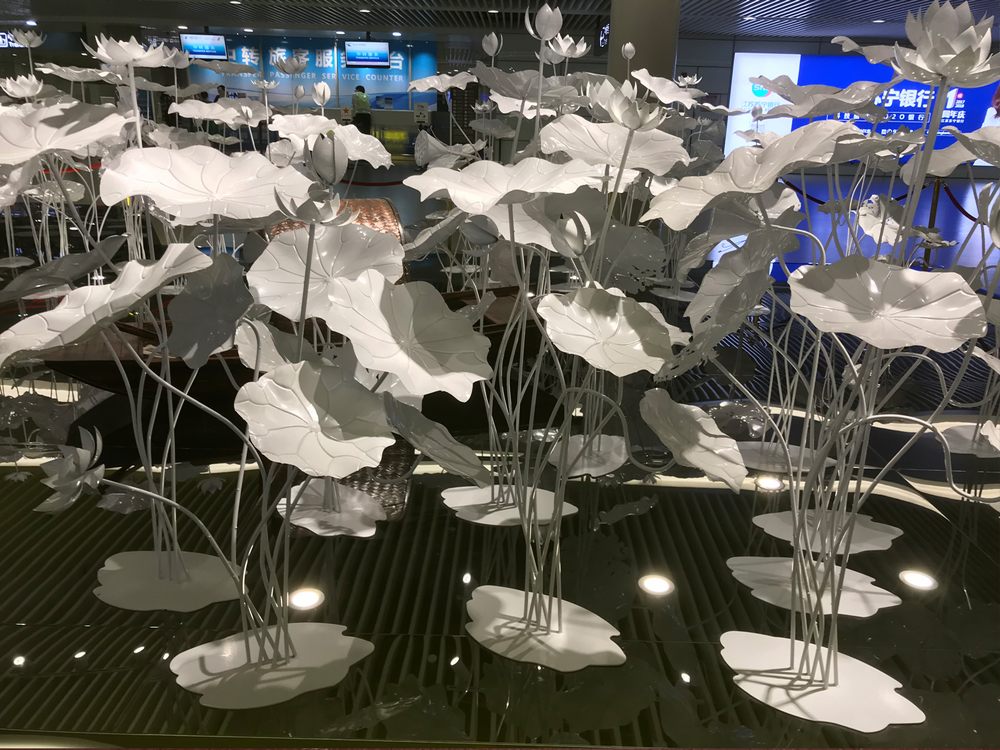
Bronze sculptures have long been admired for their durability and aesthetic appeal, but their performance in high-ionic or chemically-reactive environments is a topic of interest for artists, conservators, and collectors. Bronze, an alloy primarily composed of copper and tin, exhibits remarkable resistance to corrosion due to the formation of a protective patina layer.
In high-ionic environments, such as coastal areas with salt-laden air, bronze sculptures may initially develop a greenish-blue patina (verdigris) composed of copper carbonates and chlorides. This layer acts as a natural barrier, slowing further degradation. However, prolonged exposure to chlorides or sulfates can accelerate corrosion, leading to pitting or surface irregularities if not monitored.
Chemically-reactive environments, including industrial zones with high sulfur dioxide levels, can also affect bronze. Sulfur compounds react with copper to form copper sulfides, resulting in a dark brown or black patina. While this patina can be aesthetically pleasing, excessive sulfur exposure may weaken the sculpture’s structural integrity over time.
To enhance longevity, modern bronze sculptures are often treated with protective coatings like wax or lacquer. Additionally, alloys with small amounts of phosphorus or silicon are increasingly used to improve corrosion resistance. Regular maintenance, such as cleaning and reapplication of protective layers, is crucial for preserving bronze art in harsh conditions.
Ultimately, bronze’s resilience in challenging environments stems from its ability to form stable patinas. While no material is entirely immune to degradation, bronze sculptures, when properly cared for, can endure for centuries, even in chemically aggressive settings.