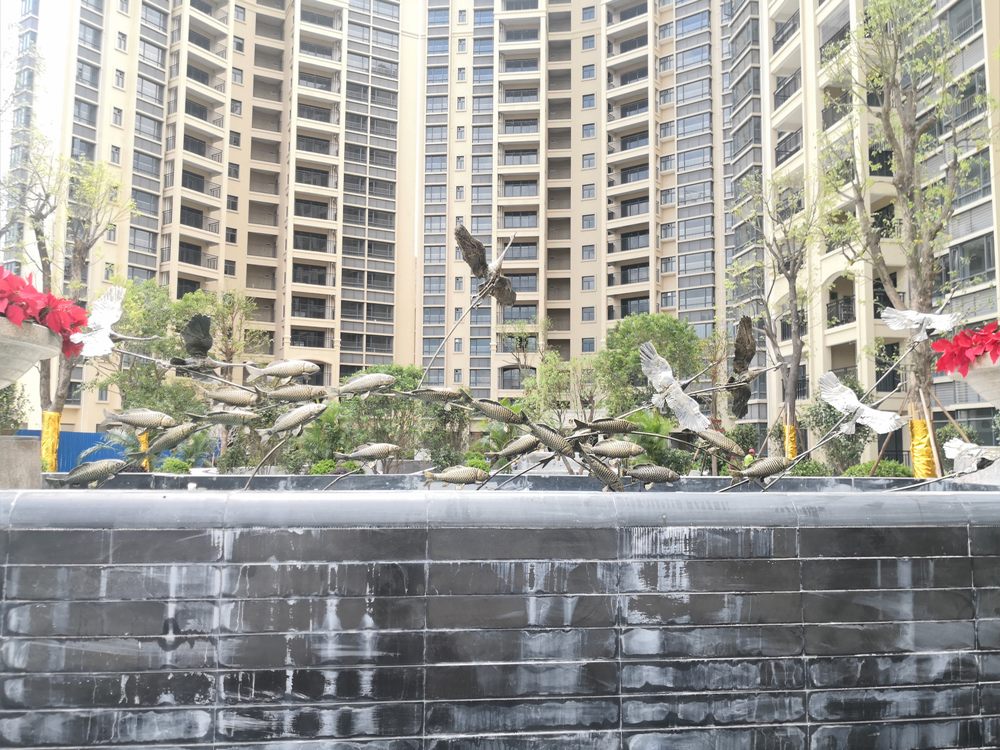
Creating hollow bronze sculptures is a centuries-old technique that allows artists to produce large, intricate works while minimizing weight and material expenses. The most common method is the lost-wax casting process, which begins with the artist crafting a detailed wax model of the sculpture.
Artists first build a clay core that forms the hollow interior of the final piece. They then apply layers of wax to create the sculpture's outer surface, carefully carving details into this wax shell. Metal rods (chaplets) are inserted to maintain the space between the core and outer mold during casting.
The wax model is then encased in a ceramic shell through multiple dipping processes. When fired, the wax melts away (hence "lost-wax"), leaving a hollow cavity. Molten bronze is poured into this cavity, filling the space between the core and outer mold. After cooling, the ceramic shell is broken away, revealing the hollow bronze sculpture.
Modern alternatives include sand casting and direct metal printing, but lost-wax remains popular for its precision. By creating hollow sculptures, artists can reduce bronze usage by 30-50%, significantly lowering material costs while making large pieces more manageable to transport and install. The technique also prevents cracking that can occur in solid castings during cooling.
Contemporary artists often combine traditional methods with digital tools, using 3D printing to create precise wax patterns. This hybrid approach maintains artistic quality while optimizing the hollow structure for both aesthetic and practical purposes.