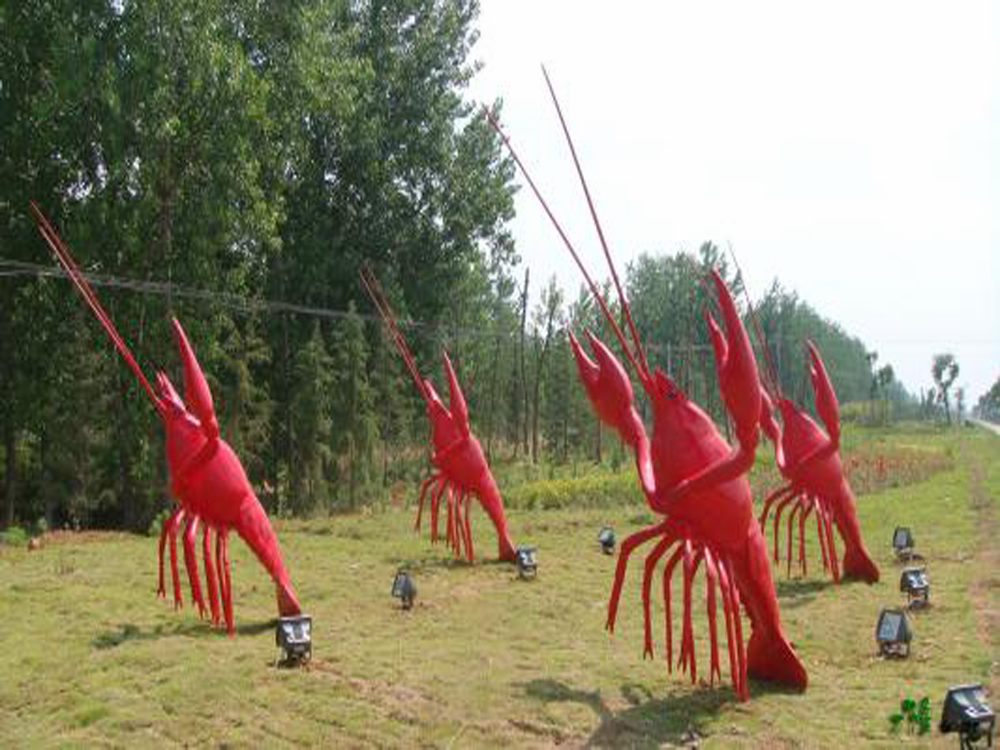
Bronze castings are widely used in art, engineering, and industrial applications due to their durability and aesthetic appeal. However, several common defects can occur during the casting process, affecting the quality of the final product.
1. Porosity: Small holes or voids caused by trapped gas or improper cooling. To remedy this, ensure proper venting during casting and use degassing agents to remove impurities from the molten bronze.
2. Shrinkage Cavities: Irregular voids formed due to uneven cooling. These can be minimized by optimizing the gating system and using chills to control cooling rates.
3. Cold Shuts: Incomplete fusion of molten metal, leading to weak seams. This defect is avoided by maintaining proper pouring temperatures and ensuring smooth metal flow.
4. Inclusions: Foreign particles embedded in the casting. Filtering the molten metal and using clean molds can prevent this issue.
5. Misruns: Incomplete filling of the mold cavity. Increasing pouring temperature or modifying the mold design can help achieve complete casting.
By understanding these defects and implementing corrective measures, manufacturers can produce high-quality bronze castings with fewer flaws. Regular inspection and process optimization are key to minimizing these issues.