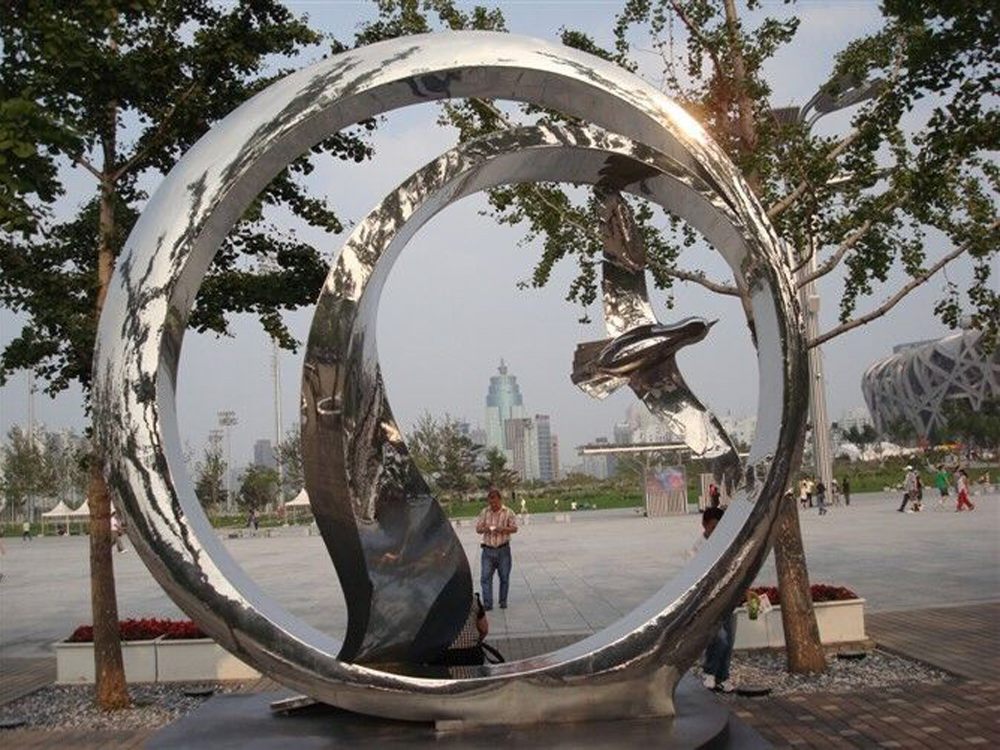
Bronze surfaces can achieve strikingly different finishes depending on whether they are hand-rubbed or mechanically polished. These two distinct methods create unique visual and tactile qualities that significantly impact the final appearance and performance of bronze objects.
Hand-rubbed bronze surfaces are crafted through meticulous manual labor, typically using abrasive compounds and cloths. This traditional technique produces a warmer, more organic finish with subtle variations that reflect the artisan's touch. The surface often exhibits a soft luster with visible tool marks that add character, making each piece truly one-of-a-kind. Hand-rubbing allows for greater control over specific areas, enabling craftsmen to highlight details or create intentional patina effects.
Mechanically polished bronze undergoes automated processes using power tools or industrial equipment. This method creates a more uniform, mirror-like finish with higher reflectivity. The mechanical approach removes nearly all surface imperfections, resulting in a cooler, more contemporary appearance. While efficient for mass production, it lacks the nuanced depth of hand-finished pieces.
Durability differs significantly between the two methods. Hand-rubbed surfaces typically retain more of the metal's natural protective oxide layer, making them slightly more resistant to environmental factors. Mechanical polishing often removes this layer entirely, requiring additional protective coatings for outdoor applications.
Cost and time factors also vary dramatically. Hand-rubbing demands skilled labor and considerable time investment, while mechanical polishing offers faster, more economical production. The choice ultimately depends on the desired aesthetic, budget, and intended use of the bronze piece.
For restoration work or high-end decorative pieces, hand-rubbed finishes often provide superior results with authentic character. Mechanical polishing proves more practical for architectural elements or functional components where consistency and efficiency are prioritized. Both methods have their place in metalworking, offering distinct solutions for different applications.