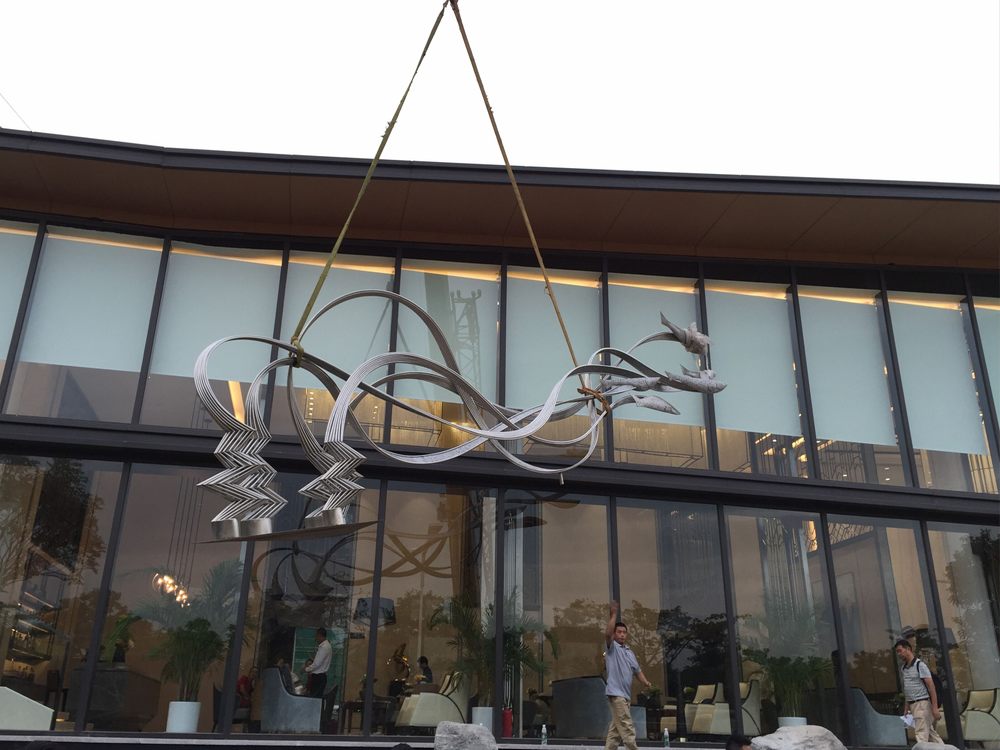
Surface blistering in bronze castings is a common defect that can compromise the quality and durability of the final product. Understanding its causes and implementing effective solutions is crucial for foundries and metalworkers.
The most frequent causes of surface blistering include:
1. Gas Entrapment: During the casting process, gases like hydrogen or oxygen can become trapped in the molten metal, forming bubbles that later appear as blisters on the surface.
2. Improper Mold Venting: Inadequate venting in the mold prevents gases from escaping, leading to pressure buildup and blister formation.
3. High Moisture Content: Moisture in molds or cores can vaporize during pouring, creating steam pockets that result in surface defects.
4. Alloy Contamination: Impurities in the bronze alloy, such as sulfur or phosphorus, can react with other elements and produce gaseous byproducts.
5. Rapid Cooling: Uneven or overly rapid cooling can trap gases and cause localized blistering.
To address these issues, consider the following solutions:
- Degassing the Melt: Use degassing agents or inert gases to remove dissolved gases before pouring.
- Optimize Mold Design: Ensure proper venting and drying of molds to eliminate moisture and allow gas escape.
- Control Pouring Temperature: Maintain optimal pouring temperatures to reduce gas solubility and improve metal flow.
- Use High-Quality Alloys: Source clean, contaminant-free bronze alloys to minimize reactive gas formation.
- Post-Casting Treatments: Heat treatment or mechanical finishing can sometimes mitigate minor blistering defects.
By addressing these root causes and implementing preventive measures, manufacturers can significantly reduce surface blistering and improve the overall quality of bronze castings.