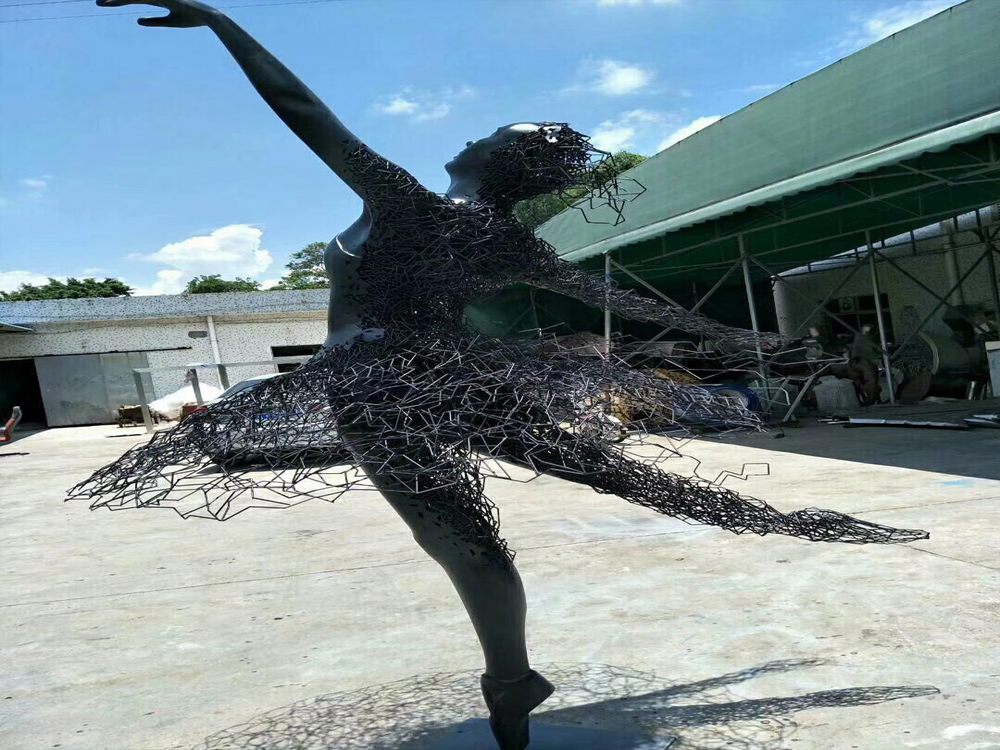
Welding bronze in large installations presents unique challenges due to the material's properties and the scale of the project. One major issue is bronze's high thermal conductivity, which dissipates heat quickly, making it difficult to maintain a consistent welding temperature. This can lead to incomplete fusion or weak joints.
Another challenge is bronze's susceptibility to oxidation during welding. The formation of oxides on the surface can weaken the weld and compromise the structural integrity of the installation. Proper shielding gases and flux materials are essential to minimize oxidation.
Large installations also require precise alignment and support to prevent warping or distortion as the bronze pieces expand and contract during welding. Tack welding and jigs are often used to maintain alignment, but this adds complexity to the process.
Additionally, bronze's varying alloy compositions can affect weldability. Some alloys are more prone to cracking or porosity, requiring specialized welding techniques and filler materials.
Finally, the sheer size of large installations can make welding logistically challenging. Access to all weld points may require scaffolding or specialized equipment, increasing time and labor costs. Overcoming these challenges demands expertise, careful planning, and the right tools to ensure durable and aesthetically pleasing results.