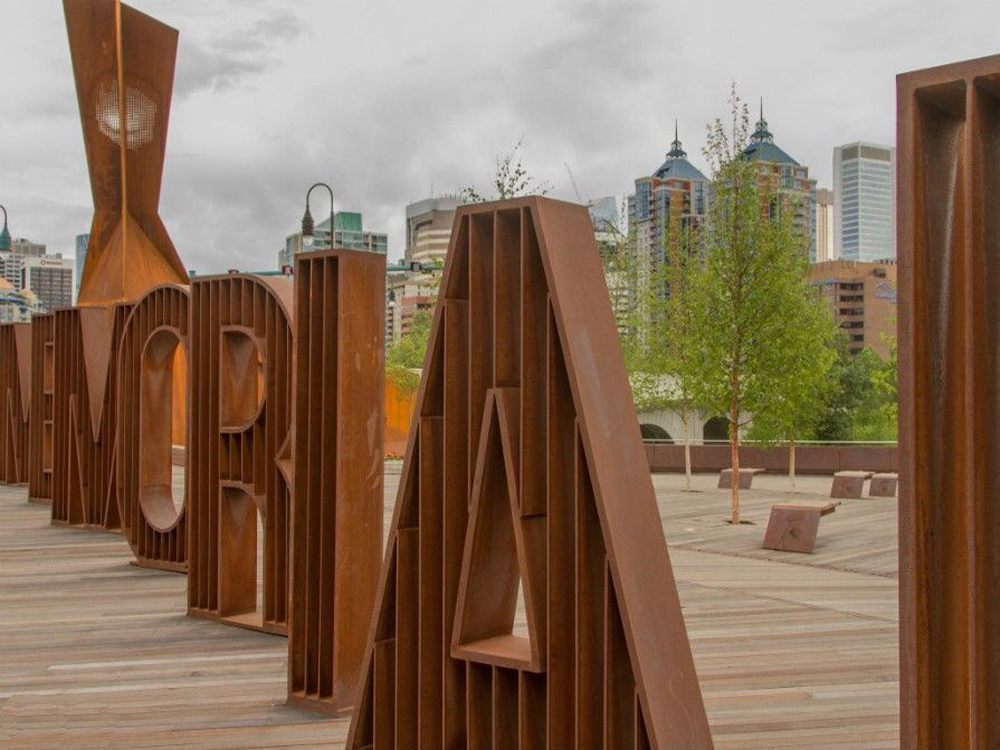
The pricing of bronze sculptures involves a complex calculation that balances artistic value with practical expenses. Artists typically consider three primary cost components when setting prices for their bronze works: material expenses, labor investment, and market positioning.
Material costs form the foundation of pricing. Bronze itself is an expensive alloy, with prices fluctuating based on copper and tin market values. The quantity of metal required depends on the sculpture's size and thickness, with larger pieces consuming significantly more material. Additional material expenses include high-quality casting sand, wax for lost-wax casting, and finishing patinas.
Labor constitutes the most variable cost factor. The creation process involves multiple specialized stages: initial clay modeling, mold making, wax working, ceramic shell formation, metal pouring, chasing, and final patination. Each step requires different skill sets and time investments. Complex designs with intricate details may demand hundreds of hours from skilled artisans. Artists must account for both their own creative time and any assistant labor costs.
Beyond direct costs, pricing reflects artistic reputation and market demand. Established artists command higher prices due to their proven track record, while emerging talents may price more competitively. Limited edition pieces carry premium pricing compared to open editions. Gallery commissions (typically 30-50%) also factor into retail pricing calculations.
Smart artists maintain detailed cost records to ensure pricing covers expenses while remaining market-appropriate. Many use formulas incorporating material costs multiplied by a labor factor, then adjusted for their market position. The most successful sculptors balance fair compensation with collector accessibility, creating sustainable pricing strategies that support their artistic practice.