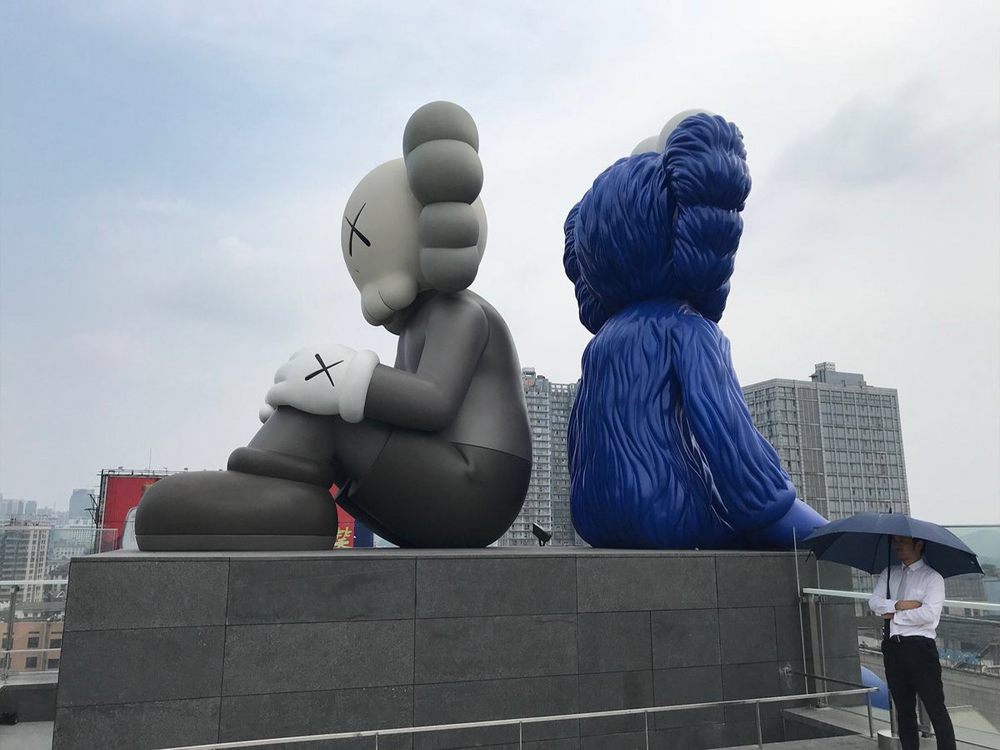
Bronze sculptures are prized for their durability and artistic value, but over time, appendages such as arms, legs, or decorative elements can break due to accidents or wear. Repairing these damages requires specialized techniques to ensure structural integrity and aesthetic harmony.
1. Welding and Brazing: For clean breaks, TIG (Tungsten Inert Gas) welding or brazing is often used to reattach broken pieces. Skilled artisans carefully align fragments and apply heat to fuse the bronze without compromising details.
2. Patching with Bronze Fillers: Smaller cracks or missing sections can be filled with bronze epoxy or molten metal patches. These fillers are shaped and textured to blend seamlessly with the original sculpture.
3. Mechanical Fastening: In cases where welding isn’t feasible, dowels or pins made of bronze or stainless steel are inserted to reinforce the joint before adhesive is applied.
4. Patina Matching: After repairs, the restored area must be chemically treated to match the sculpture’s original patina. This involves applying acids, heat, or pigments to replicate aged or colored finishes.
5. Support Structures: For heavy or load-bearing appendages, internal armatures may be added to prevent future stress fractures.
Each repair demands a balance of artistry and metallurgical knowledge to preserve the sculpture’s historical and visual authenticity. Consulting a professional conservator ensures the best results for valuable or antique pieces.