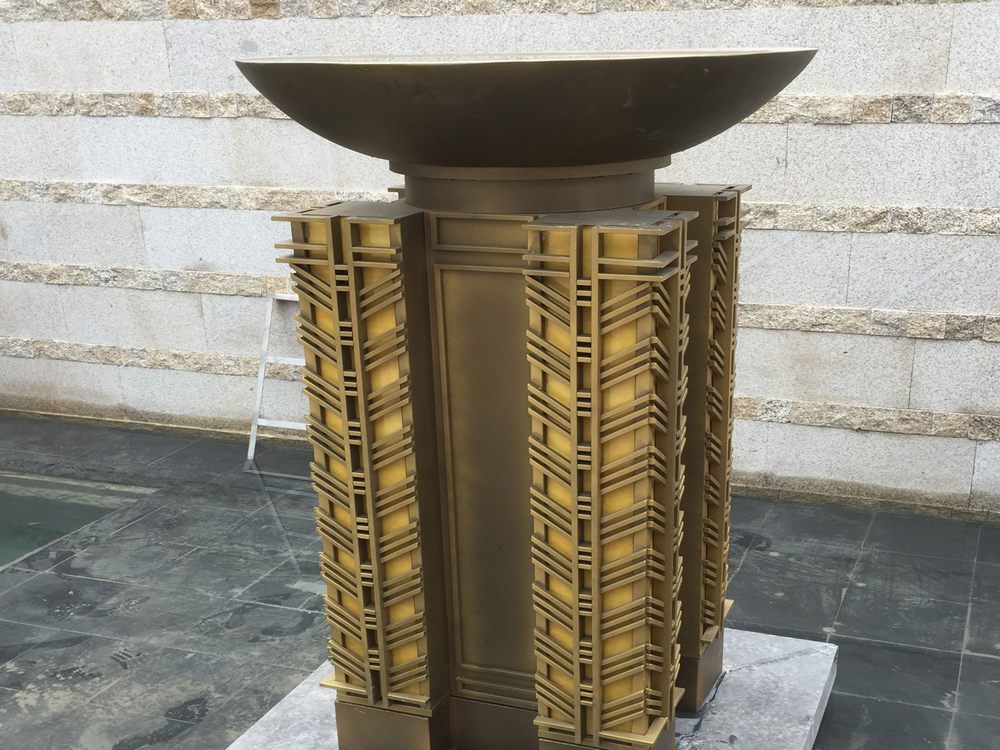
Creating bronze sculptures with delicate, thin elements presents unique challenges that test the limits of artistic skill and technical precision. One major hurdle is the casting process—molten bronze flows best through thicker sections, making it difficult to fill slender areas without defects like air bubbles or incomplete pours. Artists must carefully design molds and sprues to ensure even metal distribution.
Structural integrity is another concern. Thin bronze elements are fragile and prone to cracking or warping during cooling or handling. Reinforcing these sections without compromising aesthetics requires innovative engineering, such as internal armatures or strategic thickening.
Finishing delicate details also demands exceptional craftsmanship. Polishing or patinating thin areas risks damaging them, so artists often use specialized tools and techniques to preserve fine features. Additionally, environmental factors like temperature fluctuations can cause stress fractures over time, requiring protective measures in display settings.
Despite these challenges, mastering delicate bronze work allows for breathtaking artistic expression, pushing the boundaries of what's possible in metal sculpture.