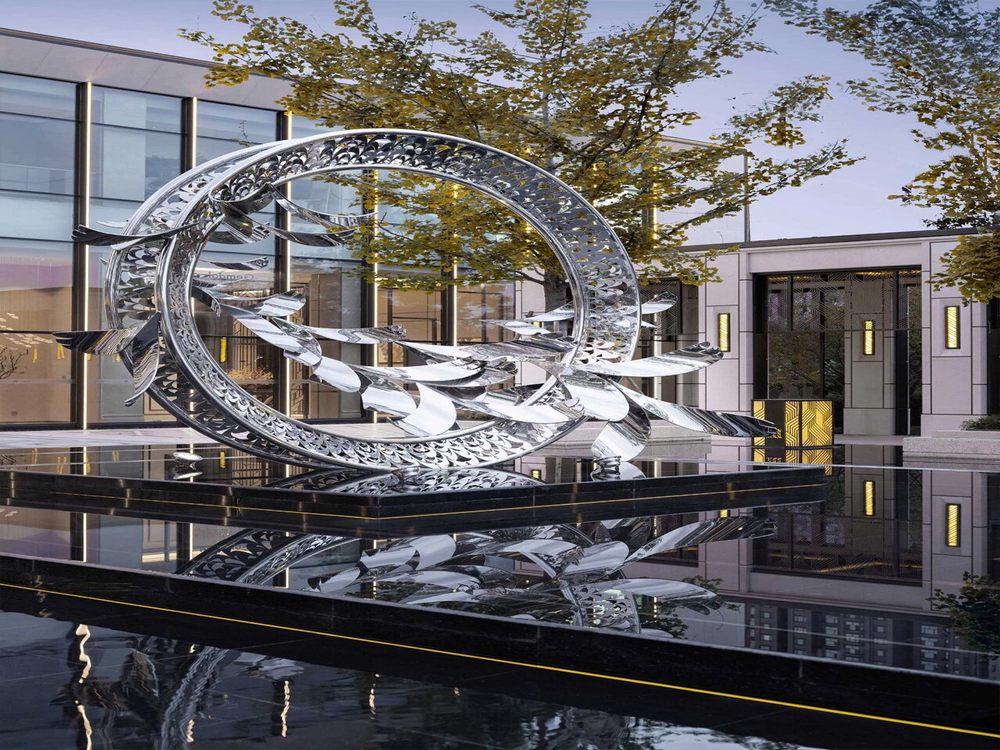
Creating bronze sculptures with extreme proportions or scales presents unique challenges that test the limits of artistic and technical expertise. One primary difficulty lies in the material itself—bronze's weight and structural integrity become critical when scaling up. Large sculptures require meticulous engineering to prevent collapse or distortion, often demanding internal armatures or supports.
The casting process also grows exponentially complex. Traditional lost-wax techniques struggle with oversized pieces, as molten bronze must flow evenly through massive molds without cooling too quickly, risking cracks or incomplete fills. Artists frequently resort to segment casting, joining multiple sections—a process vulnerable to visible seams or misalignments.
Proportional extremes introduce aesthetic hurdles. Exaggerated features may appear distorted when translated into three dimensions, requiring advanced anatomical knowledge to maintain visual harmony. Additionally, patina application becomes inconsistent across vastly different surface areas, complicating color uniformity.
Environmental factors compound these issues. Outdoor installations face thermal expansion, wind resistance calculations, and long-term weathering concerns not present in smaller works. Transport and installation of monumental pieces often require custom solutions, from specialized rigging to on-site assembly.
Despite these obstacles, sculptors employ innovative solutions like 3D modeling for pre-visualization, advanced alloy blends for strength, and modular construction techniques. The resulting works push bronze sculpture into breathtaking new dimensions, proving that artistic vision can triumph over material constraints.