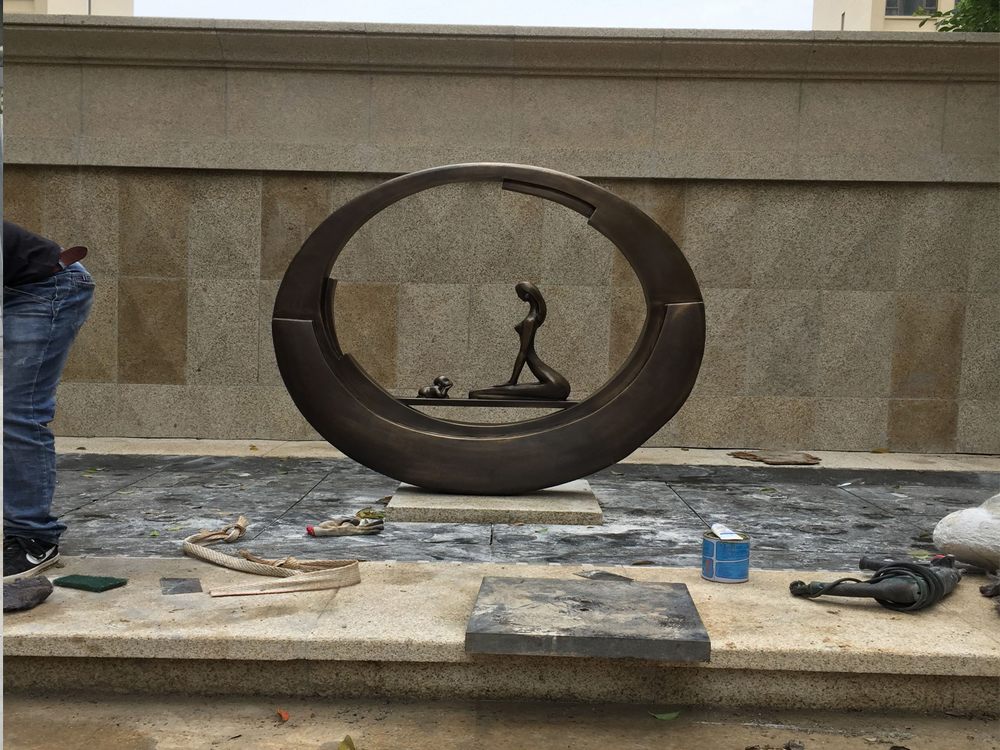
The creation of multi-part bronze sculptures has evolved dramatically with modern technology and artistic innovation. One groundbreaking approach combines traditional lost-wax casting with digital design, allowing artists to create intricate interlocking components with perfect precision. Contemporary sculptors are increasingly using 3D printing to produce wax patterns or even ceramic molds directly, enabling previously impossible geometric complexity in bronze assemblies.
Another revolutionary method involves modular casting systems, where standardized connection points allow for infinite reconfiguration of sculptural elements. Some avant-garde artists are experimenting with "cold connection" techniques using industrial fasteners or magnetic joints between bronze pieces, creating dynamic sculptures that can be rearranged.
The most cutting-edge practitioners are developing hybrid processes that merge bronze with other materials. One notable innovation is the use of bronze-plated 3D printed metal frameworks, combining the strength of modern alloys with bronze's classic appearance. Other artists are pioneering reactive bronze surfaces that develop unique patinas where different cast components meet.
These innovative approaches are redefining what's possible in bronze sculpture, offering artists unprecedented freedom in scale, complexity, and interactivity while maintaining the material's timeless appeal. The future of multi-part bronze work lies in this fusion of ancient craftsmanship with 21st-century technology.