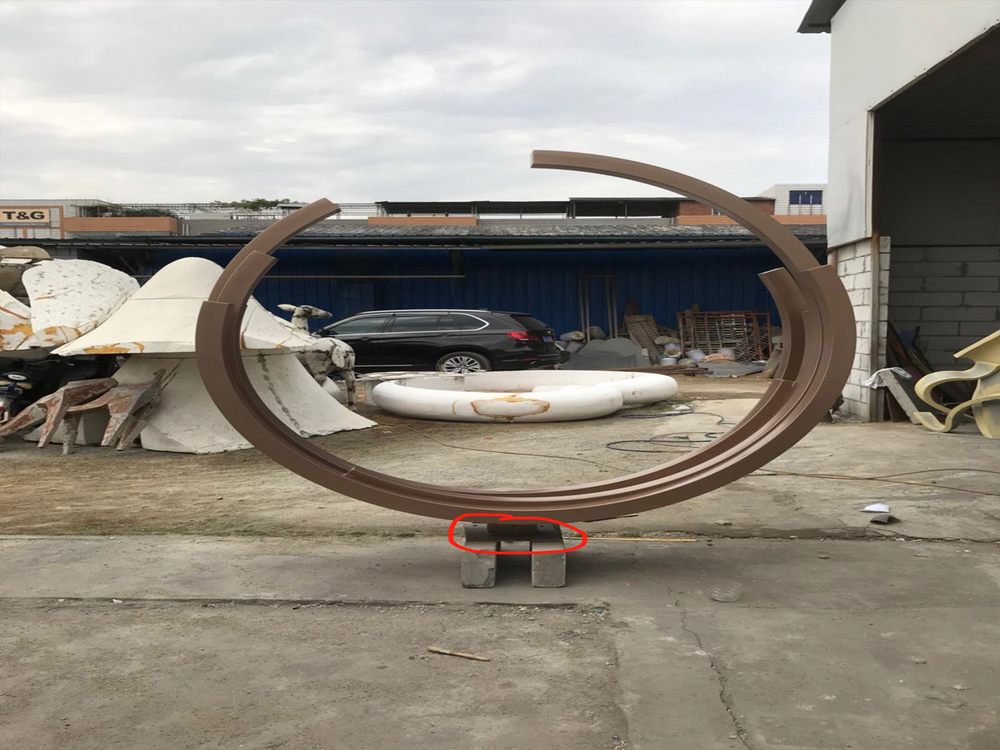
Creating bronze sculptures with extreme cantilevers is a remarkable feat that blends artistry with engineering. However, it presents several unique challenges.
First, structural balance is critical. Bronze is a dense material, and cantilevers—unsupported extensions—require precise weight distribution to prevent tipping or collapse. Artists must carefully calculate the center of gravity, often using counterweights or hidden supports.
Second, the casting process becomes more complex. Traditional lost-wax casting may struggle with thin or elongated sections, risking cracks or deformities. Advanced techniques like sectional casting or 3D-printed molds are often needed, increasing time and cost.
Third, thermal stress during cooling can warp delicate cantilevered sections. Artists must account for shrinkage rates and cooling times to maintain the sculpture’s integrity.
Lastly, long-term durability is a concern. Cantilevers are prone to stress fatigue, especially in outdoor installations where weather and vibrations take a toll. Reinforcements like internal armatures or alloy adjustments are often necessary.
Despite these challenges, bronze sculptures with extreme cantilevers captivate audiences with their daring forms, showcasing the artist’s mastery over both creativity and physics.