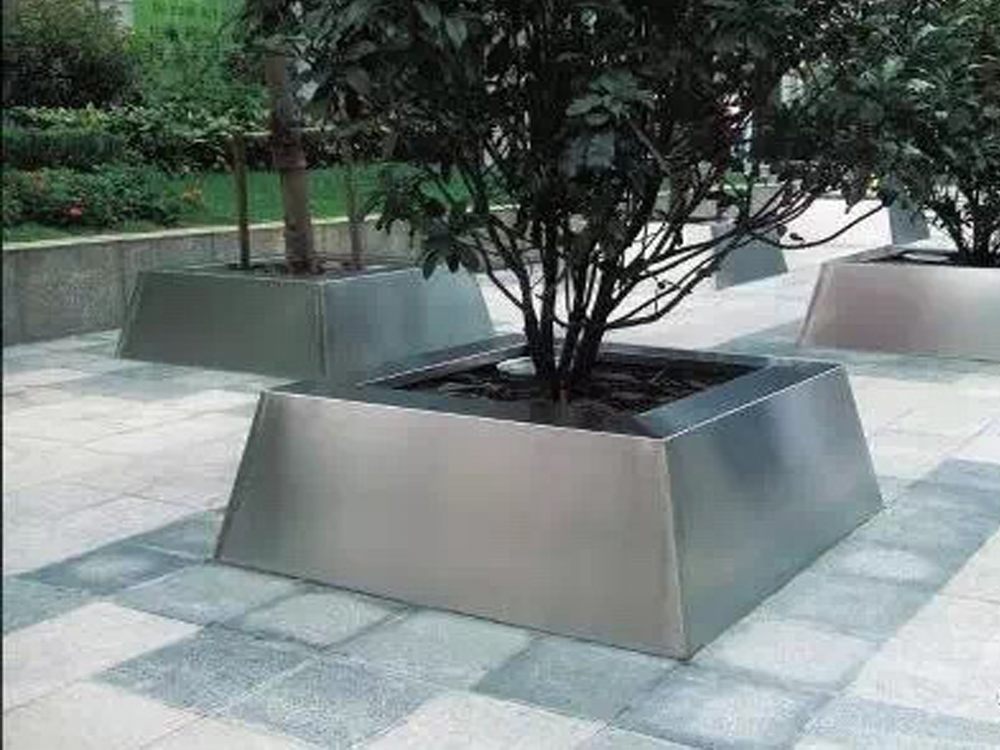
Creating bronze sculptures with intricate, unsupported extensions presents a unique set of challenges for artists and foundries alike. One of the primary difficulties lies in maintaining structural integrity—thin or extended sections of bronze are prone to cracking or collapsing under their own weight during the casting process. The metal's natural shrinkage as it cools further complicates matters, often distorting delicate details.
Artists must carefully plan armatures or internal supports to prevent warping, yet these can interfere with the final aesthetic. The lost-wax casting method, commonly used for bronze, requires precise mold-making to capture fine details without trapping air bubbles that could weaken the sculpture. Additionally, the weight distribution of unsupported elements demands expert engineering to prevent long-term stress fractures.
Patina application becomes trickier on complex extensions, as uneven oxidation may occur. These technical hurdles push sculptors to innovate while respecting bronze's inherent limitations—a fascinating intersection of artistry and metallurgy.