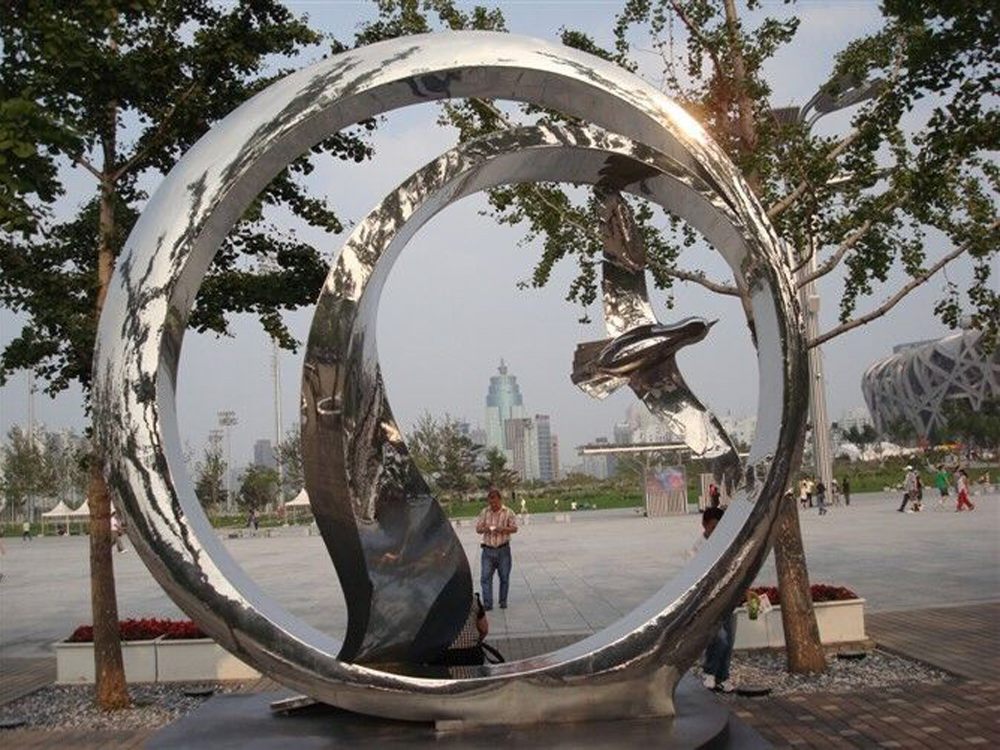
Bronze casting is a revered ancient technique, but even experienced artisans encounter defects that compromise quality. The most common issues include porosity, where trapped gas creates tiny holes, often due to improper venting or moisture in molds. Shrinkage defects occur as bronze cools unevenly, causing cracks or depressions—controlled cooling rates help mitigate this. Inclusions, foreign particles embedded in the metal, stem from contaminated molds or alloys. Misruns happen when molten bronze fails to fill the entire mold, usually from low pouring temperatures. Cold shuts appear as visible seams where metal flows meet but don't fuse properly. Each defect has specific prevention methods: degassing molten bronze reduces porosity, while proper gating systems ensure complete mold filling. Understanding these flaws empowers casters to produce higher quality bronze artifacts with consistent structural integrity.