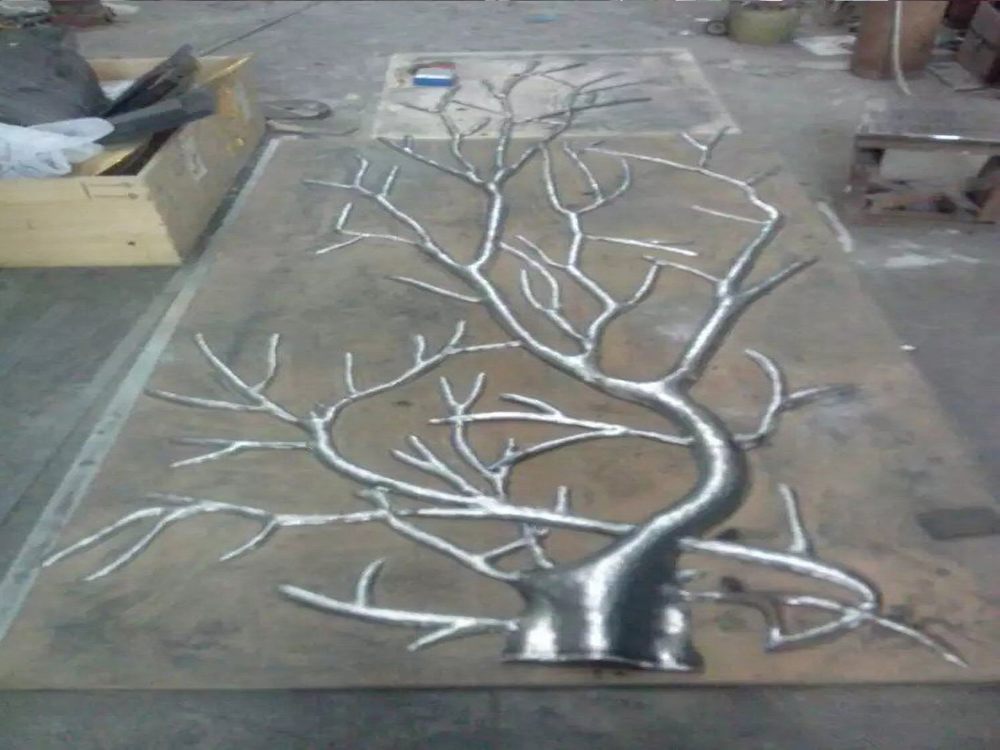
Creating ultra-thin bronze sculptures that maintain structural integrity presents unique challenges for artists and metalworkers alike. The primary difficulty lies in bronze's natural properties - while it's a durable alloy, extreme thinness compromises its inherent strength. Artists must carefully balance thickness, often working with sections as thin as 1-2mm, which requires exceptional casting precision to avoid weak points or fractures.
The casting process itself becomes exponentially more difficult with thinner designs. Traditional lost-wax methods may fail to properly fill ultra-fine cavities, leading to incomplete pours or air bubbles that weaken the structure. Many sculptors now employ advanced techniques like vacuum-assisted casting or centrifugal methods to ensure complete metal distribution in delicate areas.
Thermal stress presents another significant hurdle. Bronze contracts as it cools, and uneven cooling in thin sections can cause warping or cracking. Artists often use specialized cooling chambers or heat-resistant molds to control this process. Some incorporate internal armatures or strategic thickening in hidden areas to reinforce delicate protruding elements without compromising the visual thinness.
Finishing ultra-thin works requires equal precision. Traditional polishing and patination techniques can be too aggressive, potentially damaging the sculpture's integrity. Many artists develop custom tools and gentler methods specifically for thin bronze pieces. Despite these challenges, successful ultra-thin bronze sculptures represent remarkable achievements in both artistic vision and metallurgical expertise, pushing the boundaries of what's possible in metal art.