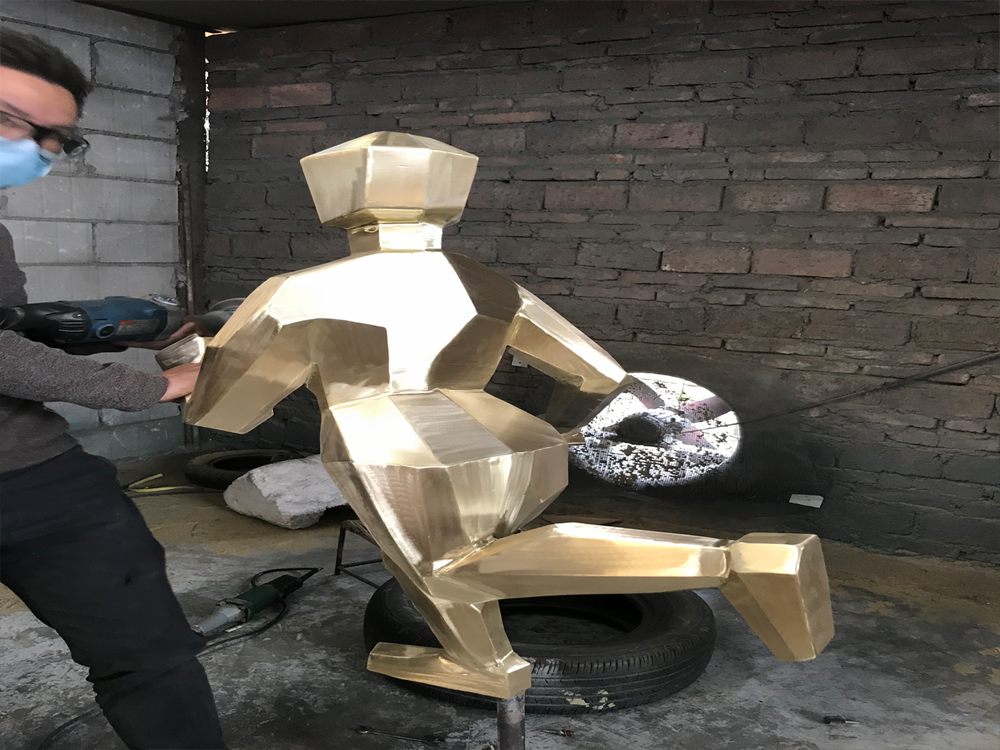
Bronze casting is a revered technique in metalworking, with centrifugal and vacuum-assisted methods standing out for their unique advantages. Understanding their differences helps artisans and manufacturers choose the right approach for their projects.
1. Process Mechanism
Centrifugal bronze casting relies on rotational force to distribute molten metal into molds. The spinning motion ensures even filling, ideal for symmetrical pieces like rings or cylindrical artifacts. In contrast, vacuum-assisted casting uses suction to draw molten bronze into intricate molds, reducing air pockets and enhancing detail precision—perfect for complex designs.
2. Material Quality
Centrifugal casting often produces denser metal structures due to centrifugal force compacting the material. However, vacuum-assisted casting minimizes oxidation and porosity by eliminating air, resulting in smoother surfaces and finer finishes.
3. Efficiency and Cost
Centrifugal casting is faster for mass-producing simple shapes, while vacuum-assisted casting excels in detailed, one-off creations but requires more time and equipment. Costs vary: centrifugal setups are generally cheaper, but vacuum systems yield higher-quality outputs for premium projects.
4. Applications
Centrifugal casting suits industrial parts and jewelry with uniform shapes. Vacuum-assisted casting is preferred for artistic sculptures, dental implants, or aerospace components where precision is critical.
By weighing these factors, craftsmen can optimize their workflow and achieve superior bronze casting results.