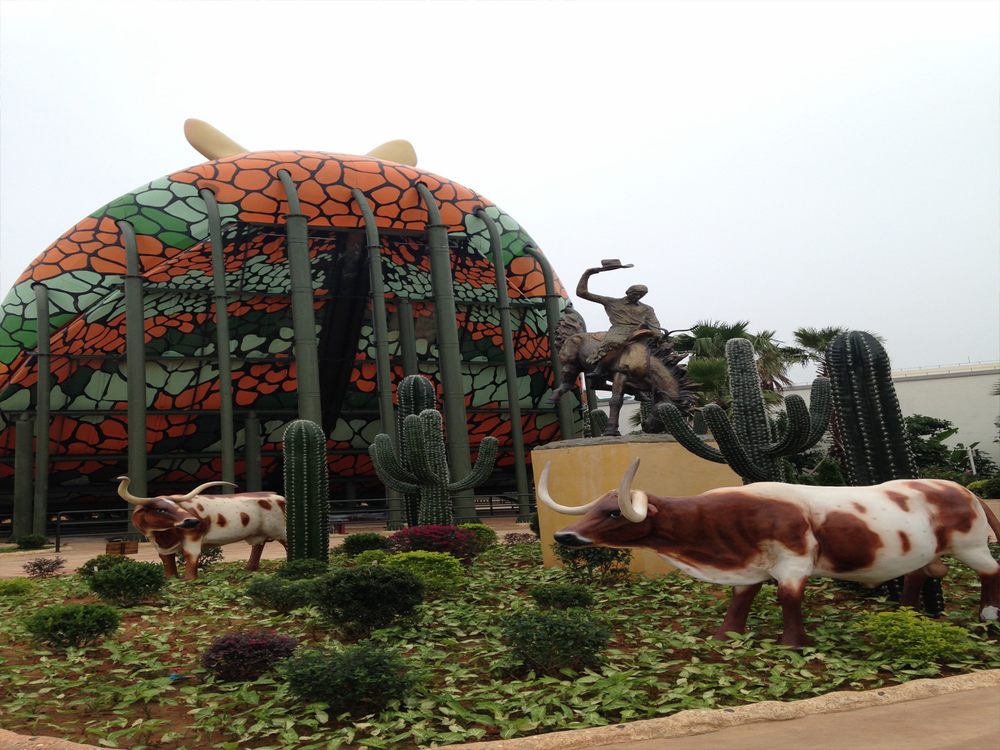
Achieving a high-gloss, mirror-like finish on bronze sculptures requires a combination of meticulous craftsmanship and specialized techniques. Artists begin by carefully sanding the bronze surface with progressively finer grits of sandpaper, often starting with 220 grit and moving up to 2000 grit or higher. This gradual refinement removes imperfections and creates an increasingly smooth base.
After sanding, polishing compounds are applied using soft buffing wheels attached to rotary tools. Tripoli compound is typically used first for initial polishing, followed by finer rouge compounds to enhance the shine. Some artists employ modern techniques like diamond paste polishing for an even more reflective surface.
The final step often involves applying a clear lacquer or wax coating to protect the polished surface from oxidation and maintain its brilliance. Some contemporary artists use electroplating with precious metals like gold or rhodium for extreme reflectivity.
For sculptures requiring both luster and artistic depth, artists may combine polished areas with matte or patinated sections, creating striking visual contrasts. The entire process demands patience and precision, as achieving a flawless reflective surface can take weeks or even months depending on the sculpture's size and complexity.
Advanced practitioners sometimes incorporate modern technology, using laser polishing or chemical brightening agents to achieve uniform reflectivity across intricate details. However, traditional hand-polishing remains the preferred method for many fine art sculptors seeking to maintain complete artistic control over their work's final appearance.