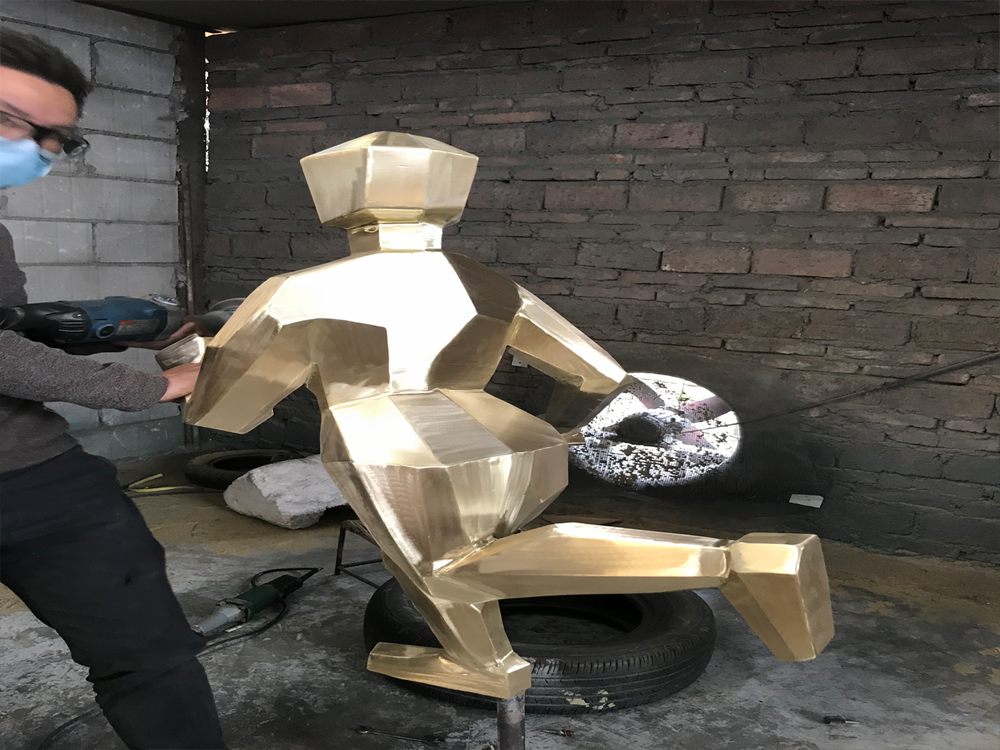
Creating miniature bronze sculptures with astonishing detail requires a combination of artistic vision, technical mastery, and painstaking craftsmanship. Artists employ several specialized techniques to achieve this remarkable level of precision.
The process typically begins with the lost-wax casting method, which allows for exceptional detail reproduction. Artists first sculpt their design in wax at a slightly larger scale than the final piece, as wax permits finer detailing than working directly in metal. This wax model is then encased in ceramic and fired, melting the wax away to leave a perfect mold for molten bronze.
For particularly intricate pieces, artists often use magnification tools like jeweler's loupes or microscopes while working. Specialized sculpting tools, some custom-made to the artist's specifications, enable the creation of minute textures and patterns. Many artists develop their own unique tools for specific detailing needs.
The bronze casting itself presents challenges - molten metal doesn't always flow perfectly into tiny cavities. Artists compensate by carefully designing channels in the mold and sometimes making multiple pours. After casting, the real artistry begins with meticulous hand-finishing. Using fine files, micro-abrasives, and delicate engraving tools, artists refine every surface and sharpen each detail.
Patina application requires equal precision, with artists using tiny brushes and controlled chemical reactions to create nuanced color variations that enhance the sculpture's depth and dimensionality. Some artists spend weeks or months on a single miniature piece, proving that in bronze sculpture, great things truly do come in small packages.