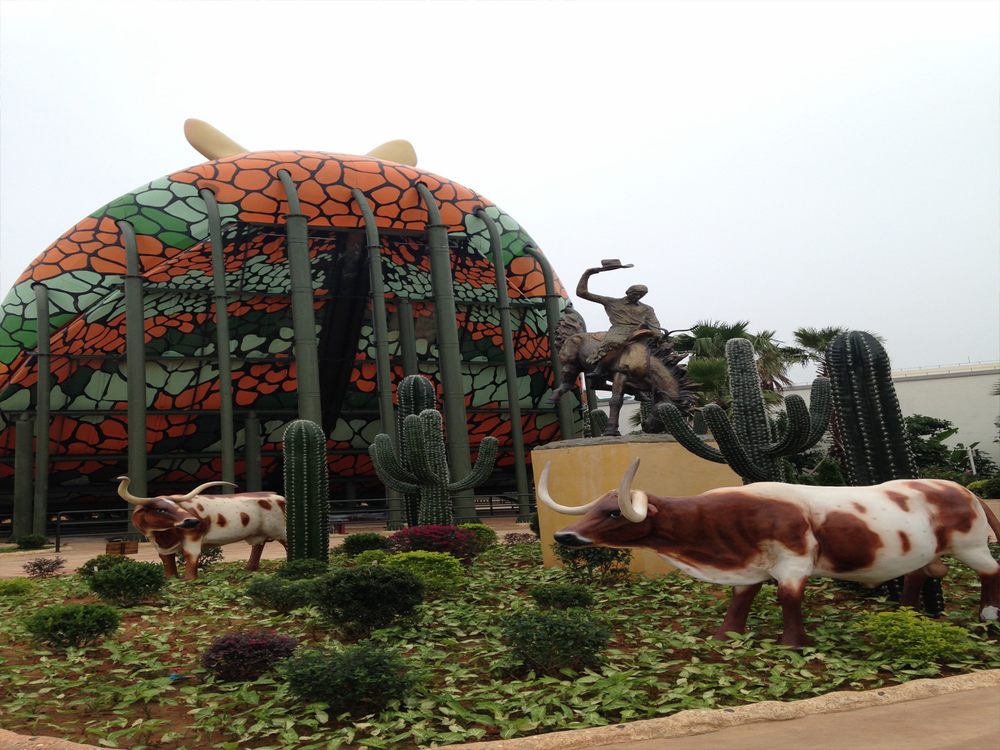
Creating bronze sculptures with openwork designs is a complex and demanding art form that requires exceptional skill and precision. One of the most significant challenges is maintaining structural integrity while achieving intricate detailing. The delicate nature of openwork designs makes the sculpture vulnerable to breakage during the casting process, requiring careful planning and execution.
Another common issue is the difficulty in achieving uniform thickness in the metal, which can lead to weak spots or uneven cooling, resulting in cracks or distortions. Artists must meticulously control the temperature and cooling rates to prevent these flaws.
Additionally, the complexity of openwork patterns often complicates the mold-making process. Traditional sand casting may not capture fine details, necessitating advanced techniques like lost-wax casting, which is time-consuming and costly.
Finally, finishing and polishing openwork bronze sculptures pose unique challenges. The intricate cavities and curves make it difficult to remove imperfections without damaging the design. Artists often spend countless hours refining the surface to achieve a flawless finish.
Despite these hurdles, the beauty and elegance of openwork bronze sculptures make the effort worthwhile, showcasing the artist's mastery and dedication to their craft.